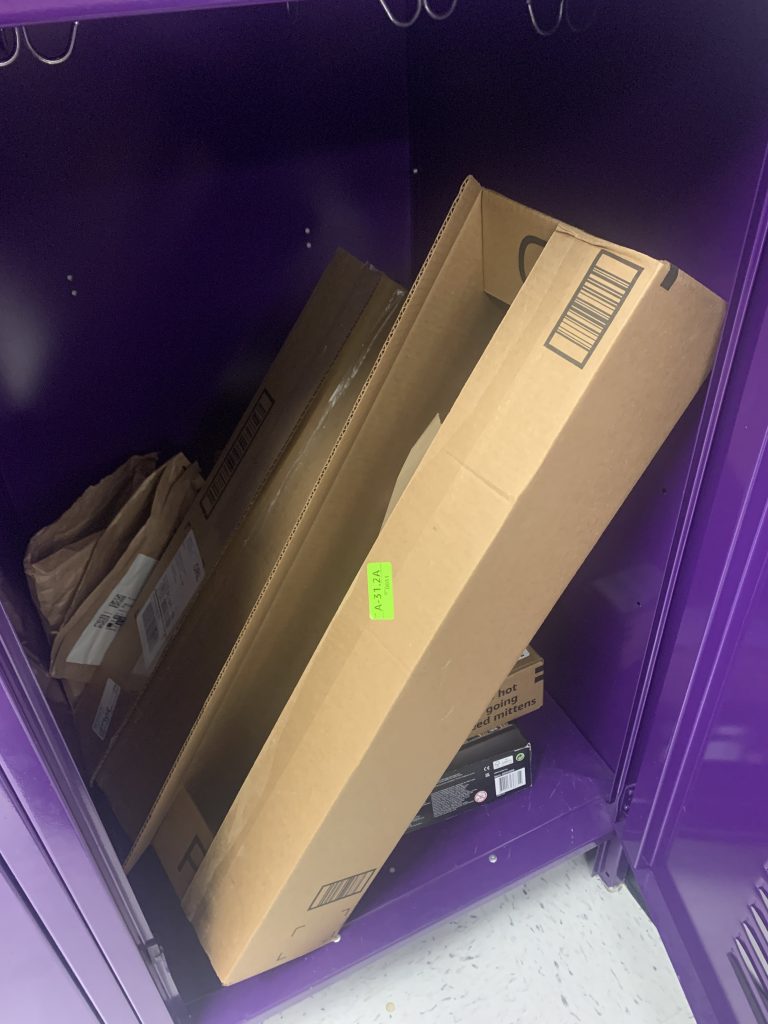
As we move into the testing phrase of the spring semester, we have most of the gantry components in and assembly has begun. Our team is working diligently to put everything together and make sure that everything fits as it should. In addition, we have been 3D printing gantry structural components and this has been going smoothly.
We are in our final stages of the sensor PCB design. The PCB design will be sent over to a PCB expert for review before we place the order. This is a critical component of our project and we are confident that it will function as intended.
The sensor device has also been verified to have the capability to be battery powered. This is an important milestone for us as it means that our device can be used in a wide range of settings without the need for an external power source.
Moving forward, our plans for the next week include finalizing and making the PCB order, considering modifications to be made for the transition from a gantry to a handheld device, and testing the gantry and stepper system function. We will continue to keep you updated on our progress. See you next week!