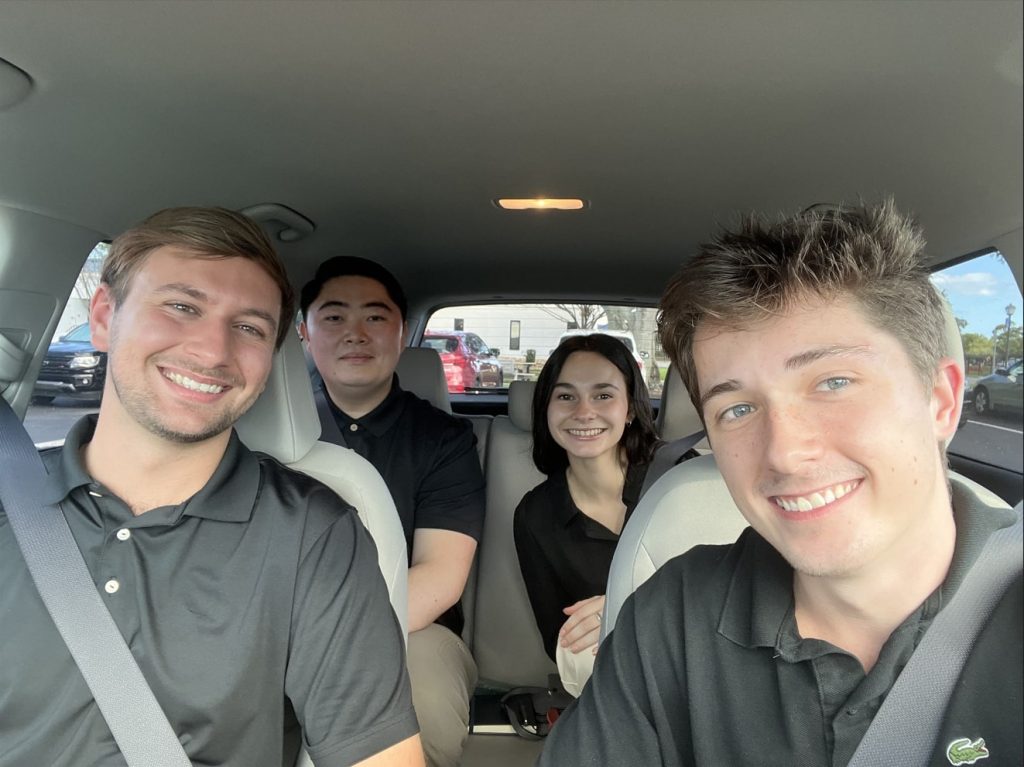
The site visit was a success, we were about to gather valuable advice from Northrop Grumman directors and engineers during our presentation, while also being provided an exclusive tour of the Northrop Grumman facility. We plan to implement all the comments we received to improve our prototype and presentation.
In preparation for prototype day on 11/15, we have compiled and ordered a list of off-the-shelf (OTS) electrical parts to start testing detector methods. Capacitance sensing is the primary detection method we are designing based on the results from our design matrix. However, we did order some metal detection sensors to test if our findings were correct during our literature review. The ordered electrical parts are expected to be delivered next week.
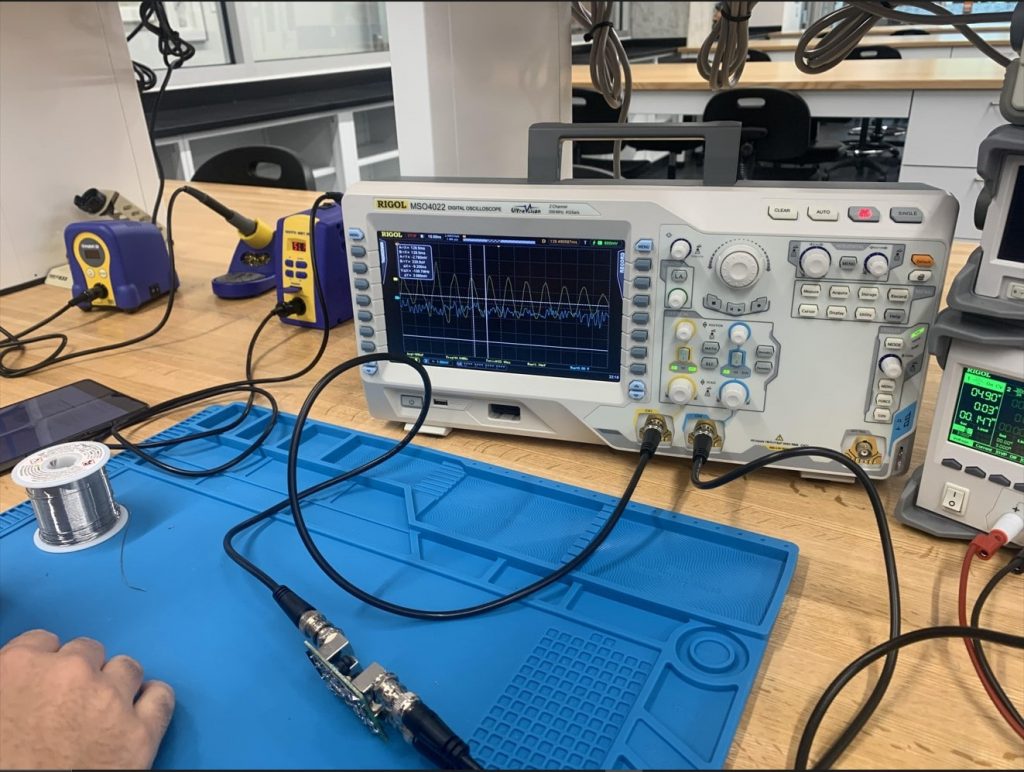
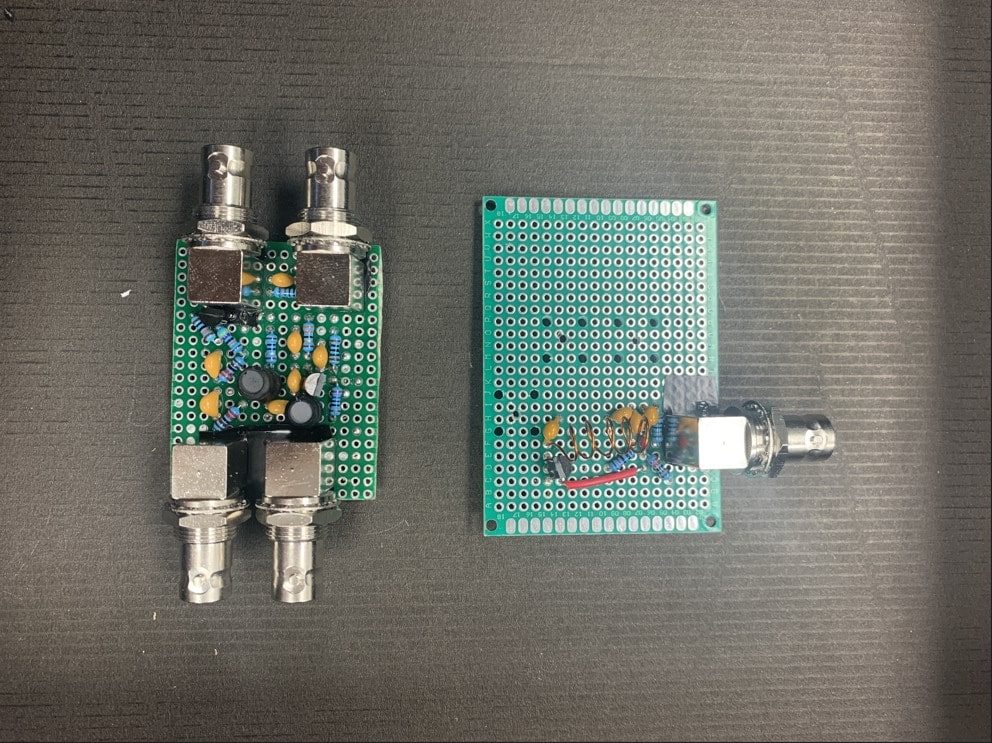
With the electrical components we had on hand, we assembled a capacitance sensing circuit consisting of a Colpitts oscillator and an RC oscillator with smoothing circuity. However, during testing, we noticed a bunch of noise within our signal, causing the result to be unreadable. The noise is most likely due to the low capacity of the oscilloscope unit.
Next week, we have scheduled a meeting with Dr. Orazem to discuss impedance as a detection method. We are also developing multiple body design concepts for our prototype, so we are not limited to one design. Come back next week to see what we have in store for our prototype design.