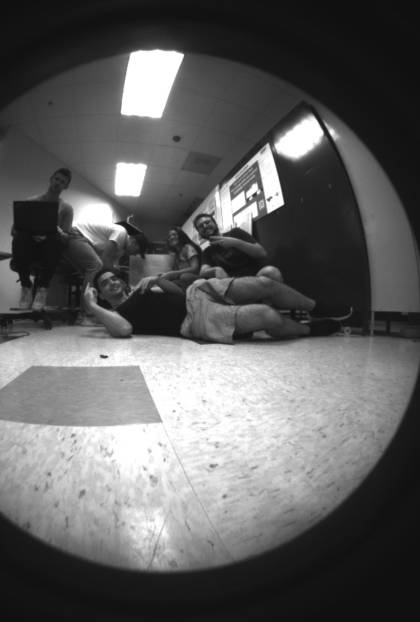
This week the Addtronics team took on presenting and giving a demonstration as part of FDR (final design review). We first gave a presentation outlining our scope of work and a broad path of how our project was accomplished throughout the course of the year. We highlighted some big failures that led to big successes and the big learning journey that we each went on individually and as a team. Following our presentation we headed to our booth which included our team poster and our live demo. The poster gave a brief overview of our project with specific items such as our scope of work, our goals, and the specifications of our design. Over to the side, we were able to show people our quadruped walking over to the mock transformer box, sitting down, and extending its arm out to lift the lid. We were able to conduct this demo repeatedly and show the live video stream inside the transformer box using the quadrupeds live video feed. Overall, we had a fantastic year learning and interacting from and with each other and are excited for what the future holds!