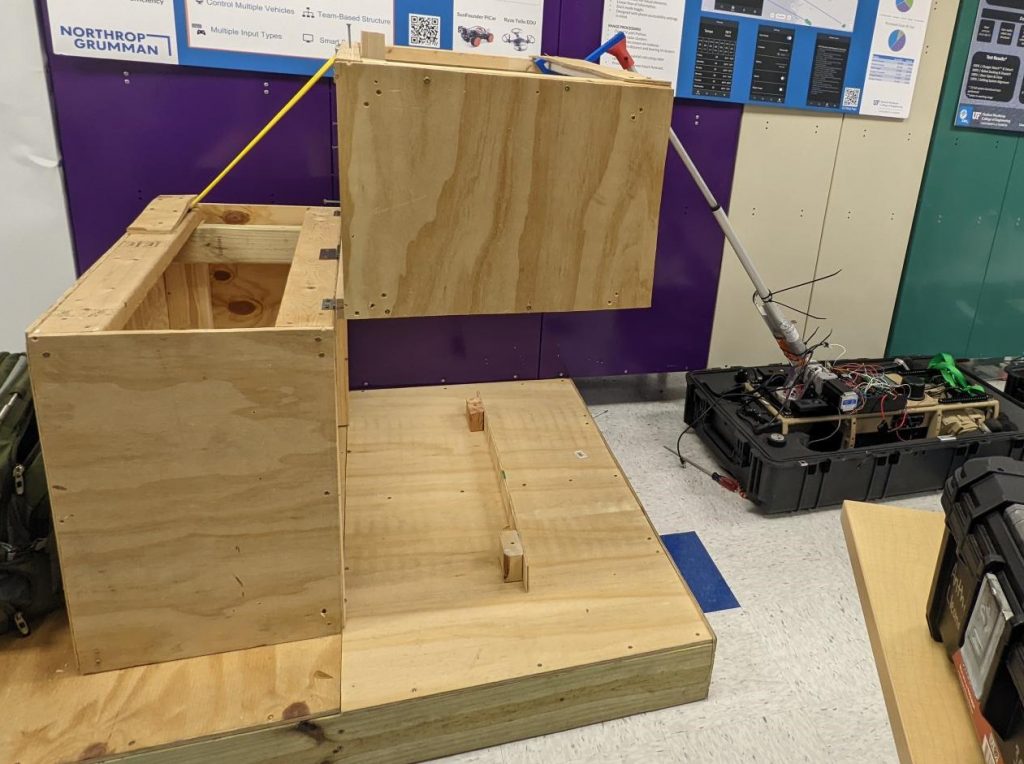
Continuing from last week the Addtronics team has worked hard to implement modifications needed (stemming from previous testing) as well as incorporating feedback and suggestions that were received during QRB2 last week. With certainty that the new motor and linear actuator worked reliably using the lightest configuration of the mock box we began adding weight to the mock box lid to simulate a payload test in a real environment (pictured above). The results showed that although the motors were now fully capable of lifting a heavier, the 3D printed components were not rigid enough to support this weight. During testing the linear actuator adapter piece and brackets used to hold it in place both broke (seen below). This corroborates our original idea that the ABS plastic parts would not be strong enough. To avoid increasing the weight of the overall assembly we have decided to create hybrid parts that are still 3D printed but have metal reinforcements, such as steel sheet metal and steel rods) within them. Several versions of these parts are being made for testing and to have extras if necessary. to lift lid (see picture). While the physical interface continues to be updated the electronics have now been successfully mounted to a perforated crossover board which avoids having to rewire and secure the electric components each time the interface is updated. This mitigates the risk of of electronics failing due to improper wiring. Additionally, this makes debugging easier as the components are removable from the rest of the assembly.
This week the team has also begun GUI testing which has shown the need to improve the network being used. The network is being modified so that the app (once deployed on the phone) can interact directly with the robotic arm and require no other intermediary device. Additionally, the team has begun exploring how to implement a “one-button-push” approach to lifting the lid that will require less skill and coordination from the user and therefore will be easier to use. Currently, the team is exploring using the camera stream on the quadruped as well as various sensors in order to implement this approach.
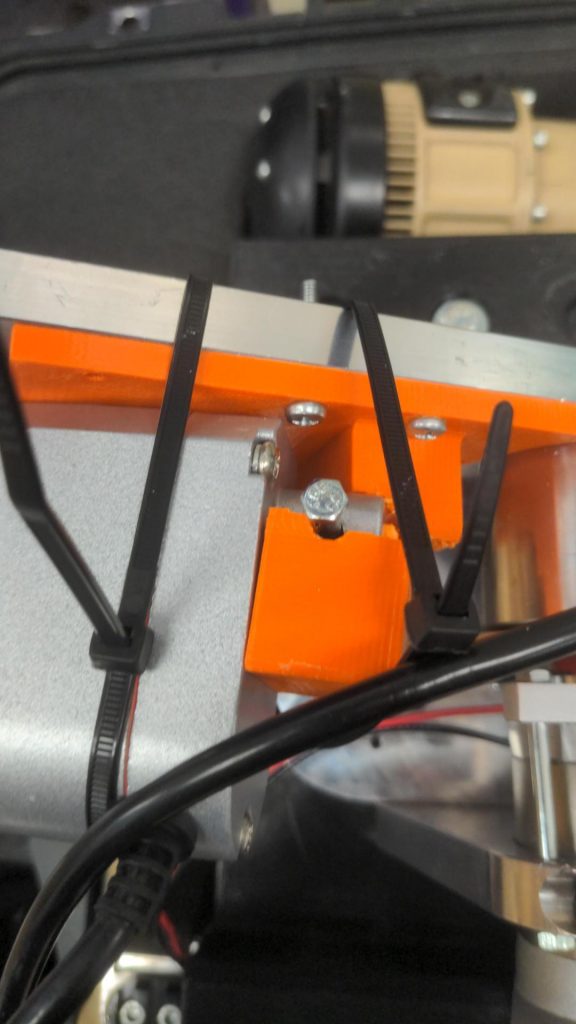
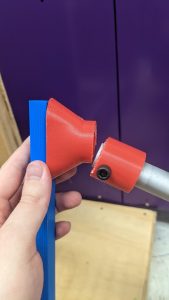