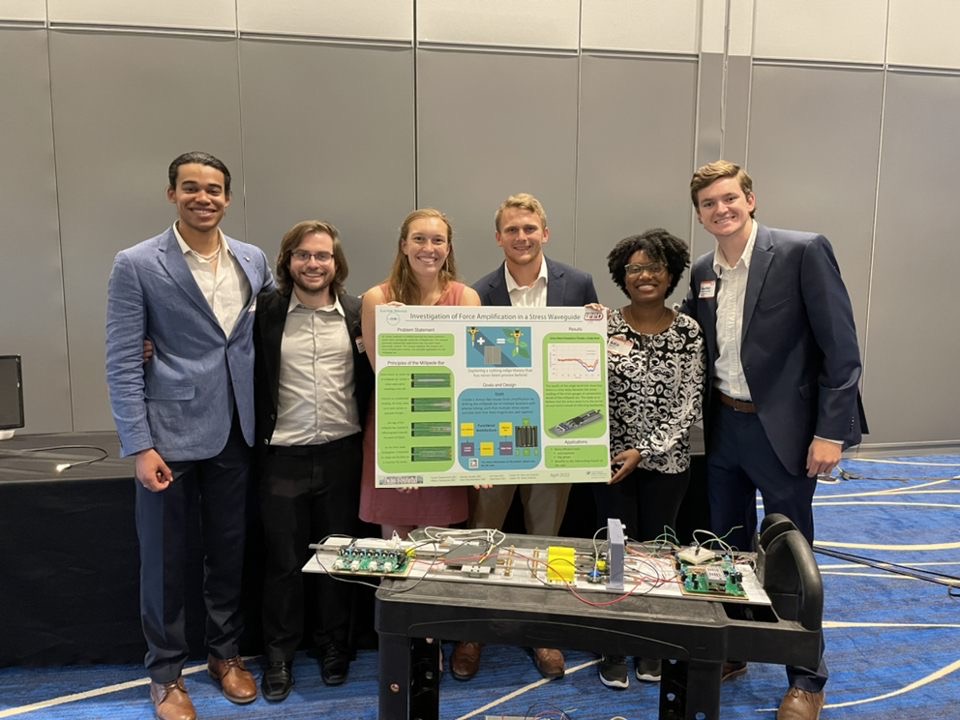
The final week of IPPD has arrived for Gator Waves! An unexpected issue (misplaced glue) in a mechanical part of the design caused unexpected test results, but this was ultimately resolved. Test data was able to be collected regarding a stress wave turning around a single bend. Unfortunately, test data regarding the constructive interference of stress waves was not able to be collected because the timing of 50 μs was not achieved. Still the final design is able to fire two striker rods simultaneously and measure the stress wave propagation at multiple points in the system.
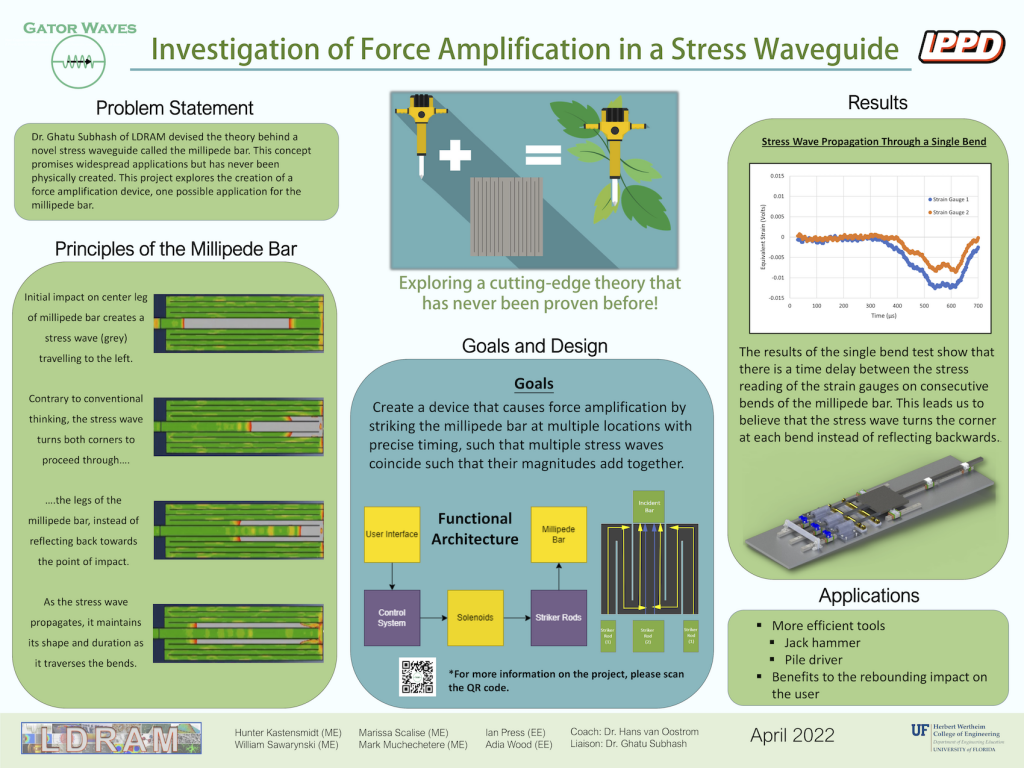
At the FDR event held on Tuesday, April 19th, our team presented what we were able to achieve this semester and also demoed the design for FDR attendees. The electrical engineers plan to spend a few more days attempting to achieve the 50 μs timing, and the team will make adjustments to the FDR report based on feedback from our liaison, Dr. Subhash. Even though all objectives of the project were not able to be achieved, our team has learned a great deal in the process and appreciates the experience IPPD has provided. Thank you!