Hello everyone and welcome back to EvapoGATOR’s weekly diary… I mean, blog. First thing’s first, refer to the pictures to understand the title.
EvapoGATOR had Prototype Inspection Day (PID) this week, and if I do say so myself, we killed it! The team transported the vacuum evaporation system from the FSHN pilot plant (near Marston) to the Reitz Union since the stainless steel frame sits atop 4 sturdy caster wheels.
Quote of the walk: “I’m not sure what that is, and I’m kinda too afraid to ask…” from a friendly student sitting at a table in the Reitz North Lawn. Then they wished us luck on our presentation when we told them what it was 🙂
We think everyone was impressed with our system, and the six judges we presented to all gave positive comments and thoughtful feedback, which the team appreciated. One of our favorite comments was from a coach who commended how much we’ve accomplished as a three-person team, and it felt good to be seen because we’ve been working extremely hard on this project, and we basically live in the FSHN pilot plant.
Anyway, all of the hard work has definitely been paying off because the system is jaw-dropping! (Okay, I’ll stop teasing, there’s a picture of the fully assembled vacuum evaporator at the bottom.) Here is some of the feedback PID judges gave for us to consider:
- Adding insulation because the system can get dangerously hot, and that could help save energy
- A more thorough understanding of the functionality of the pressure safety valve
- Using chemical engineering software to model heat transfer in the HEXs
- Possible vibration of the system
With this great feedback, EvapoGATOR was able to make some changes to our design plan and solidify our project plan from now to FDR on April 25.
Now, here are some of the things we accomplished this week after PID:
- Began applying pipe thread compound to NPT connections for a leakproof seal
- Tested first option to improve natural circulation in the evaporator
- Added a centrifugal pump under the evaporator to help with natural circulation
- Completed drafts of the lab manual and student survey for coach review
- Updated the vacuum evaporator’s 3D CAD model in Solidworks
A few of the issues we noted during PID and we’ve been working to fix are leaking components and natural circulation in the evaporator HEX. To address these, the team is sealing threaded parts to prevent leaks and decreasing the diameter for fluid flow in the evaporator, respectively. The bigger problem is natural circulation because we haven’t found the best solution yet. First, the team tried adding a copper coil and metal rod to make a smaller area and increase the pressure and bubbling, but these weren’t as effective as we had hoped.
An interesting twist though — apparently there is a right and wrong way to apply Teflon tape on threaded (NPT) parts, and if you do it the wrong way, it can absolutely ruin the threading. With that being said, there are a few connections we’re having a problem getting out of the evaporator, and we’re worried it might have ruined the threading, so we couldn’t attach anything else to those connections. To fix this problem, we are considering buying a new evaporator (shell and tube HEX) with 3/4″ NPT connections. Hopefully, the shell and tube configuration (compared to the current tube-in-tube design) will resolve the natural circulation issues we’re facing.
Now, our biggest tasks ahead include optimizing the vacuum evaporator, testing the system with grad/undergrad students, and documenting all of our work in an operations manual. We only have 3.5 weeks until FDR, but EvapoGATOR is sure we can do it!
Until then, we just have to keep working harder and smarter. Below are some of the tasks we want to accomplish next week:
- Finish outline/draft of final design report
- Finalize CAD, lab manual, and Bill of Materials (BOM)
- Design, manufacture, and assemble a tray for the thermocouple transmitter
- Finish applying pipe thread compound to NPT parts + test for leaks
- Test system under vacuum + check pressure relief valve
- Decide on a solution for labeling the system
We have a busy week ahead! These last few kinks we have to work out feel like the longest part of the process, but our team knows they’re necessary and we’re still grinding. See you all next time, and please enjoy pictures from the week!
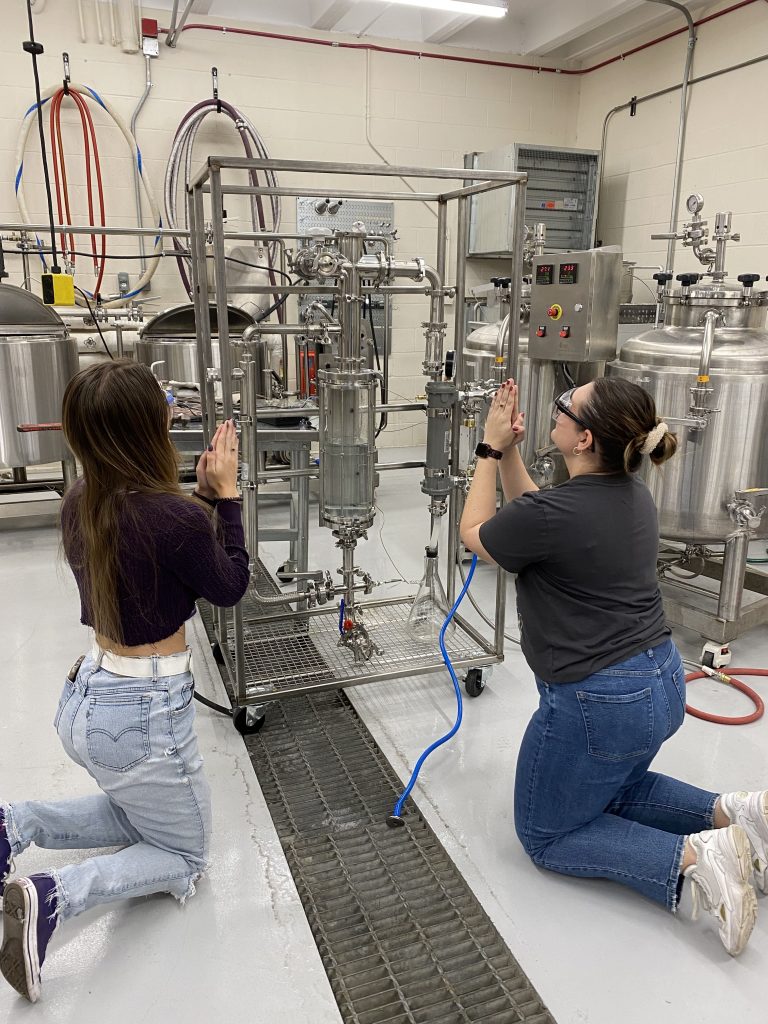
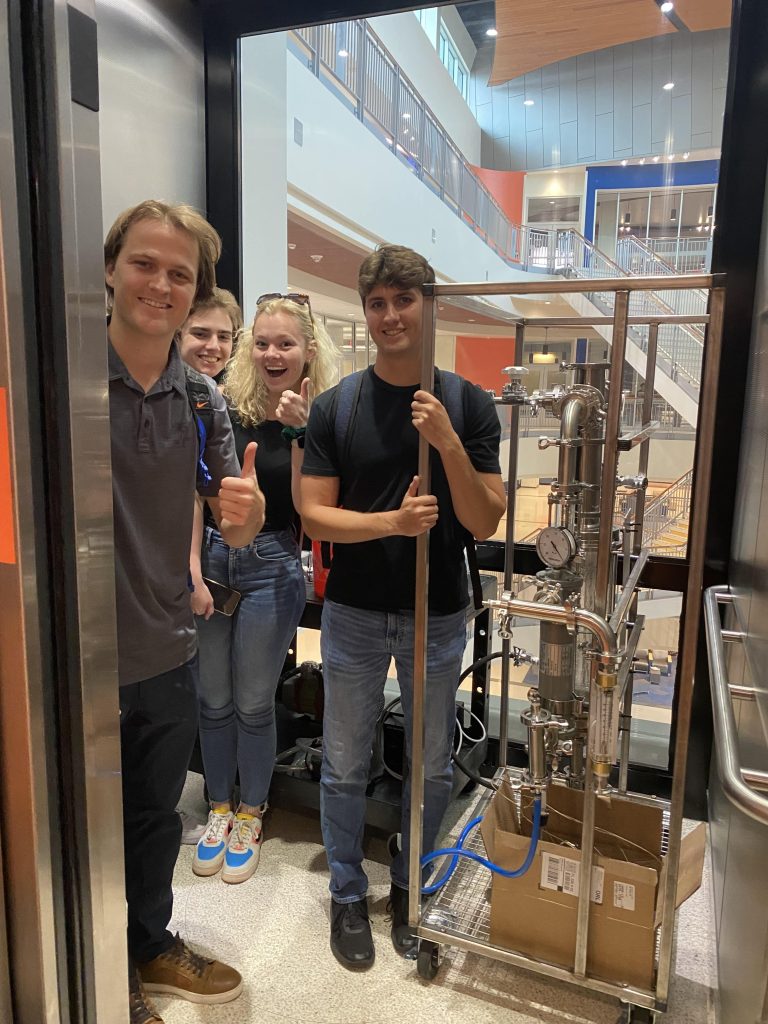
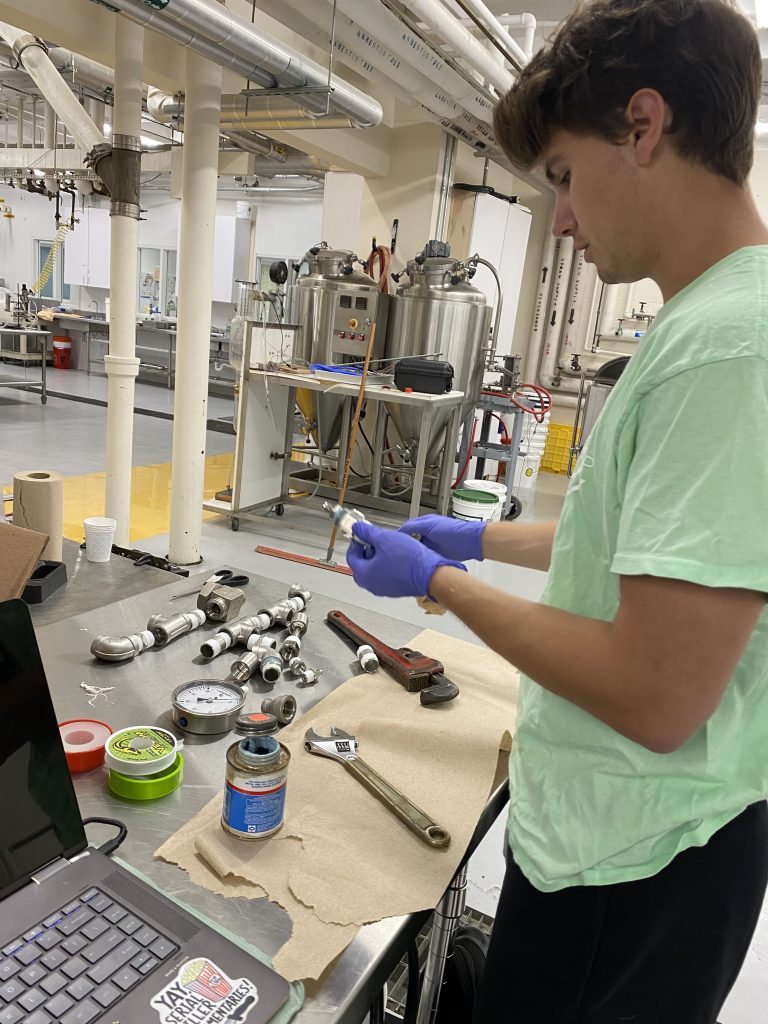
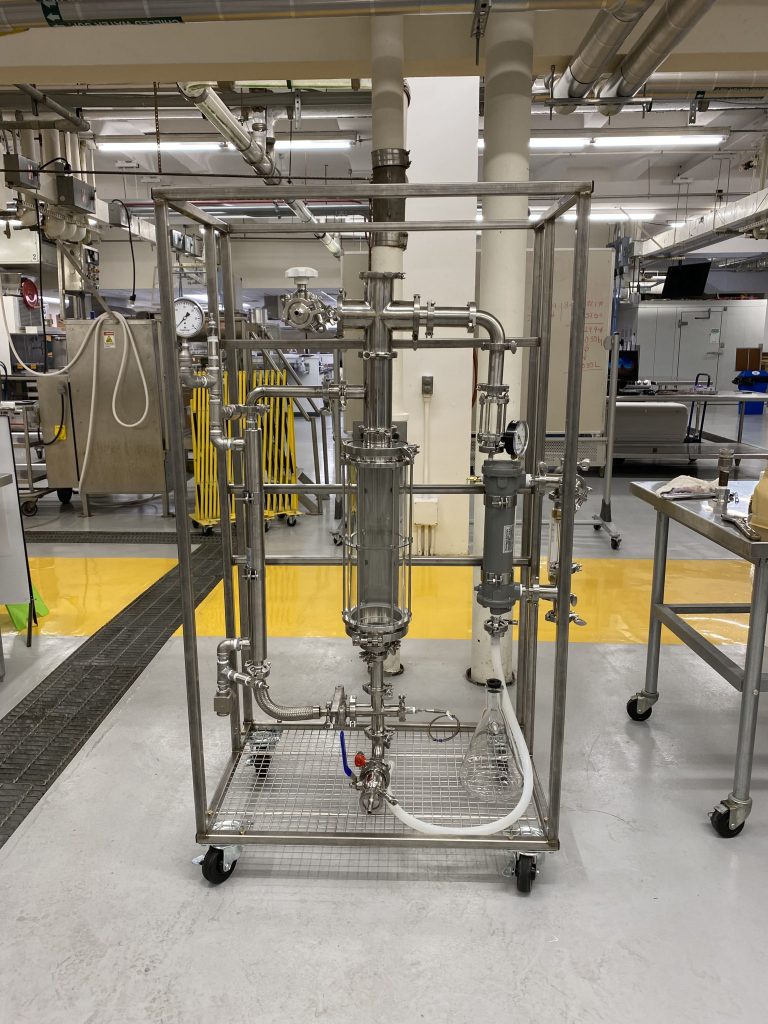
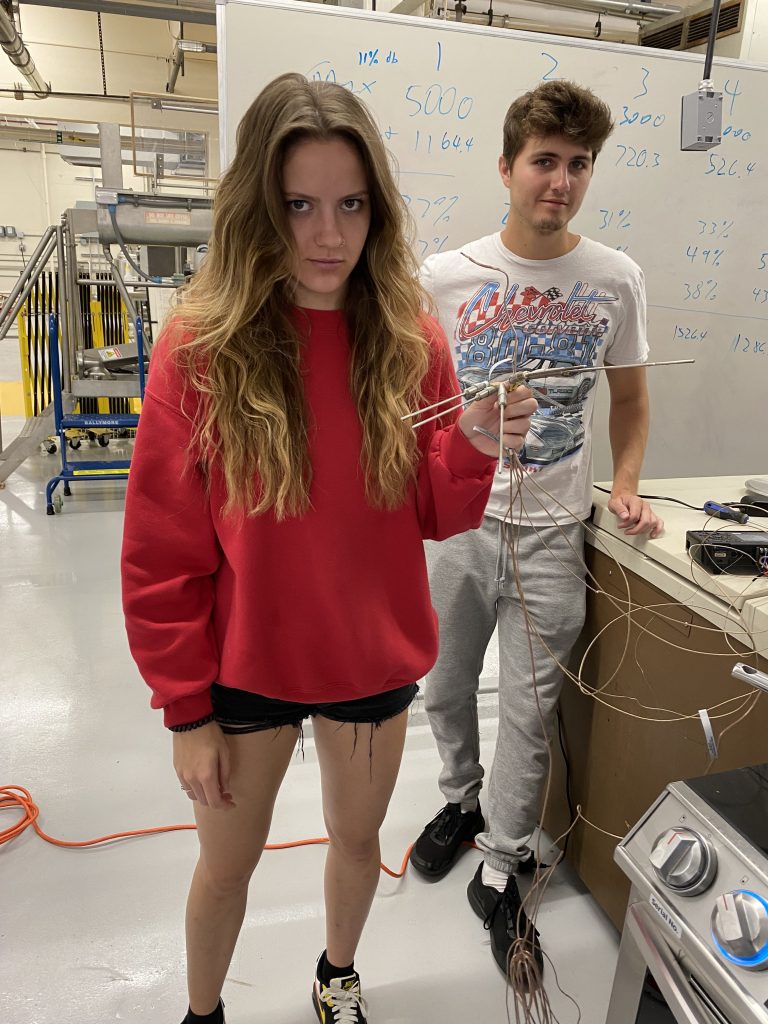