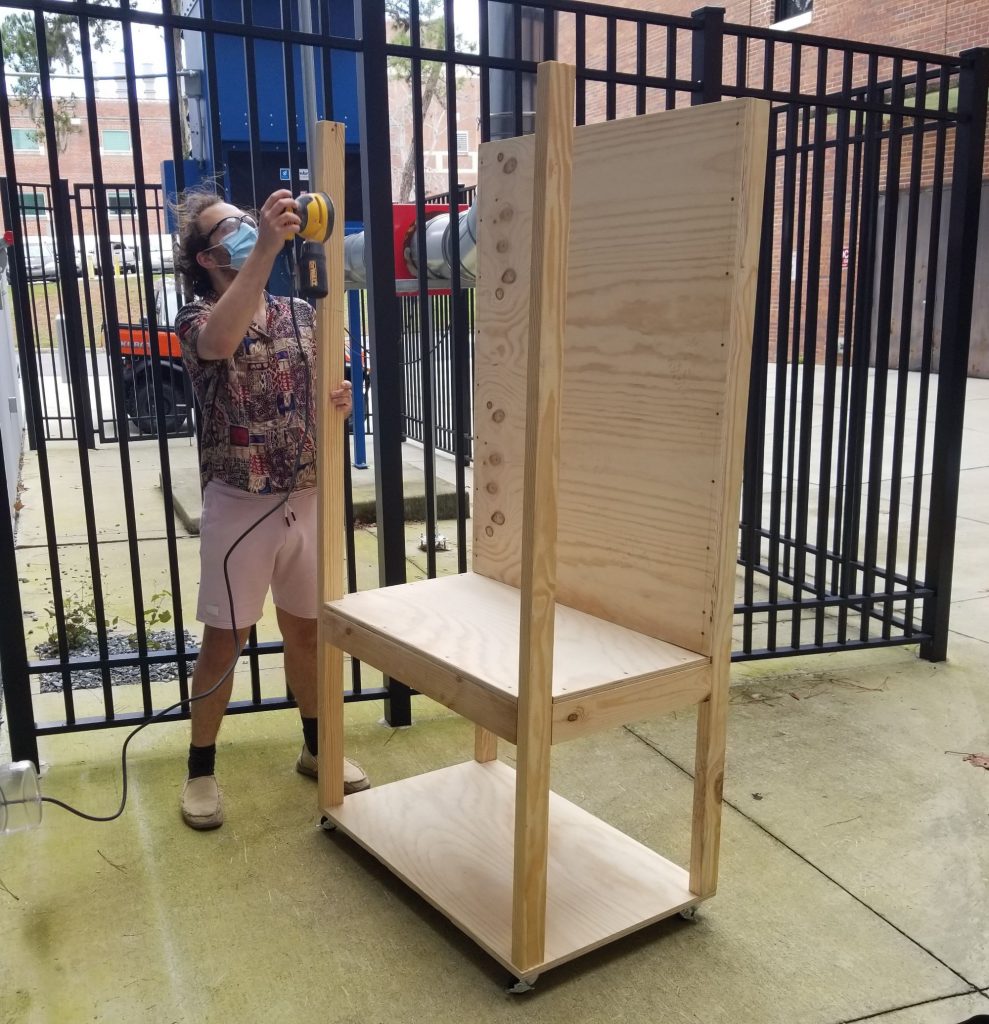
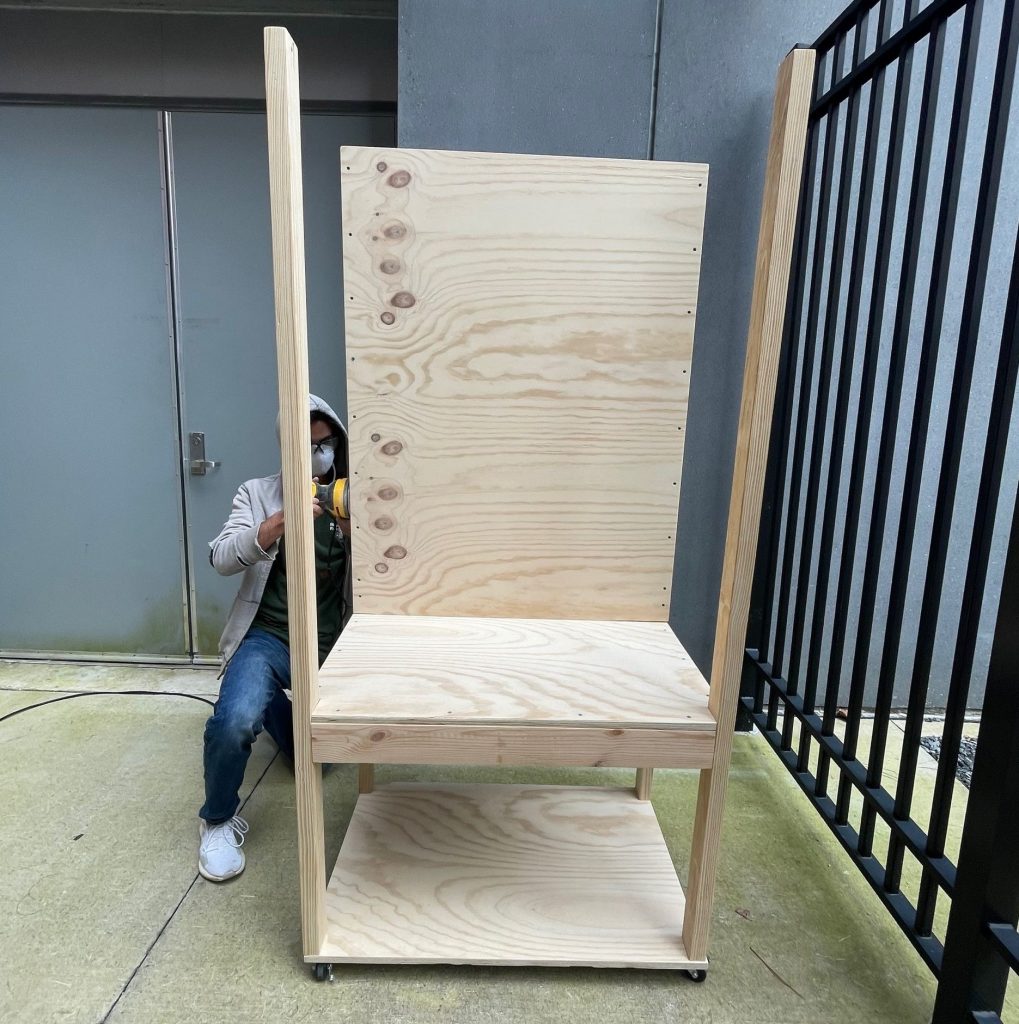
This week we’ve been 3D printing more tracks and mounting mechanisms. The Les Paul guitar is looking good now that we’ve sanded and spray-painted it. We’ve also begun coding for some of the LEDs that will be going on the machine. The CAD modeling for our rocket and Iteration light bulb mounting is finished. To help speed up 3D printing, we’ve printed these parts at UF. Our Polycrylic has arrived and is in the lab, so we can coat the frame soon and start mounting our MOIs. In the meantime, we’ve tested a mockup of Serendipity to ensure its functionality. The Cade team has been very helpful as we’ve been collaborating with them this week on color choice and getting some labels and a picture of C. J. Walker printed on PVC.