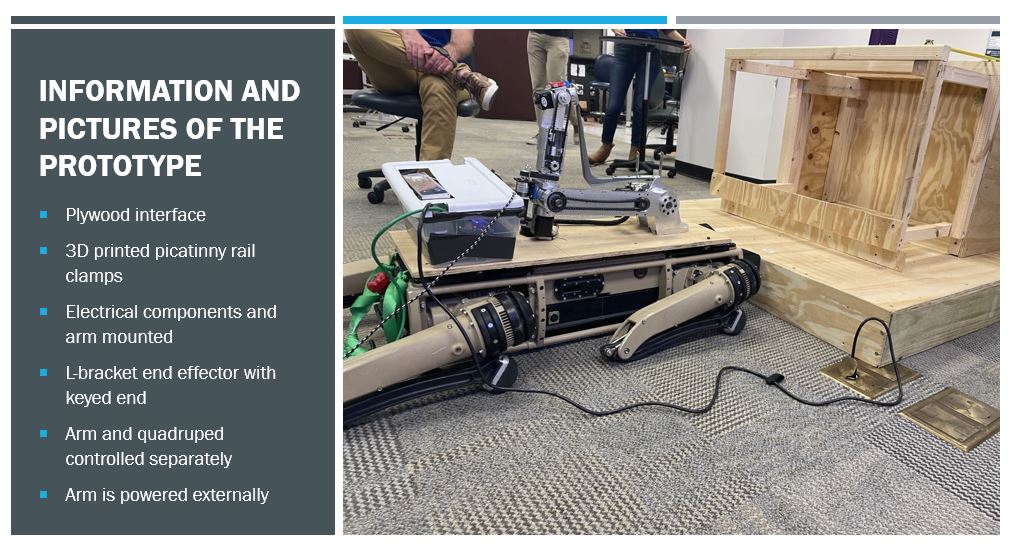
This week the Addtronics team tackled the peer reviewed Systems Level Design Report (SLDR) presentation in preparation for actual SLDR presentations that will be occurring next week. We presented general information about our project and sponsor as well as our road to prototyping and testing to showcase all the work we have done thus far. We received some fantastic feedback and questions from our peers to help us improve our presentation next week in areas such as figures, formatting, and detailed descriptions. Overall, we were able to present a lot of relevant information in a clear and concise manner that encouraged the audience to ask some great questions about our future plans and implementation strategies.
Following our feedback from prototype inspection day, the team has been hard at work with implementing new and modified designs, evaluating these changes, and planning our future work.
In terms of software there have been updates in the software used to control the arm so that it operates faster and is more maneuverable as well as updates in the Graphic User Interface (GUI) getting us closer to a more effective and user friendly design. Looking forward, we plan to combine the arm and quadruped software to be controlled through one user interface that will be accessible through a mobile device. We also plan to integrate some semi-autonomous functions of the robot such as a one button command to open the transformer lid smoothly.
As far as electronics, our electrical engineers have removed unnecessary stepper motors and stepper drivers from the arm, organized the arm’s wiring, and replaced the 2 microcontrollers originally installed on the arm with a Raspberry Pi microprocessor. The reduction of components overall reduces the complexity of the arm as well as reduces the weight loaded onto the quadruped. The wiring was organized by color coding wires and securing them using heat shrink and DIN rails which allow for easier debugging as well as provide protection from external factors. Looking forward, we plan to power the arm directly from the quadruped, change out the main lifting motor for one that can provide a greater torque, explore incorporating a linear actuator, and add sensors onto the end effector that will be used.
Lastly, our mechanical engineers have been hard at work implementing and testing some new hardware designs. So far, new metal picatinny rails have been implemented for improved rigidity of the interface mounting, new interface design and materials have been been created and purchased, respectively, and multiple new end effector designs have been manufactured. Fabrication of the new interface designs will begin soon and will be followed by extensive interface testing to determine which design best meets the project criteria. Currently, there are 4 different end effector designs with unique geometries that have been manufactured. While 3 of those end effectors have been 3D printed, one is unique in its entirely metal and modular design. The video below shows a time lapse of one of our engineers manufacturing this metal end effector which is made out of 1 inch 80/20 (extruded aluminum). Looking forward, we plan to improve the rigidity of the electronics box by reinforcing it with carbon fiber, continue testing improved versions of the most successful end effectors, and develop back up clamping methods.