Starting up and maintaining ion exchange systems involves several critical steps to ensure efficient operation. During initial startup, regeneration cycles are essential, with careful attention to valve operations and brine concentration. The system’s controller setup is tailored to each system’s specifics. Shutdown procedures mirror startup steps in reverse, crucial for system longevity. Routine maintenance includes flushing the system regularly and conducting sample testing after backwashing to maintain system integrity. Monitoring and logging normal operating conditions are vital for troubleshooting, with various parameters like pressure, flow rate, and water quality closely monitored.
On the other hand, pellet softening systems are designed for continuous operation, reducing the need for frequent startups and shutdowns. Automation streamlines operations, with minimal manual intervention required. Maintenance for these systems is low due to automation and fewer moving parts, mainly scheduled for upgrades or comprehensive cleaning. Operational efficiency ensures a steady supply of softened water, with continuous monitoring of parameters like pH, hardness levels, and turbidity to maintain water quality. Waste management in both systems involves proper disposal of byproducts, emphasizing sustainability and environmental responsibility.
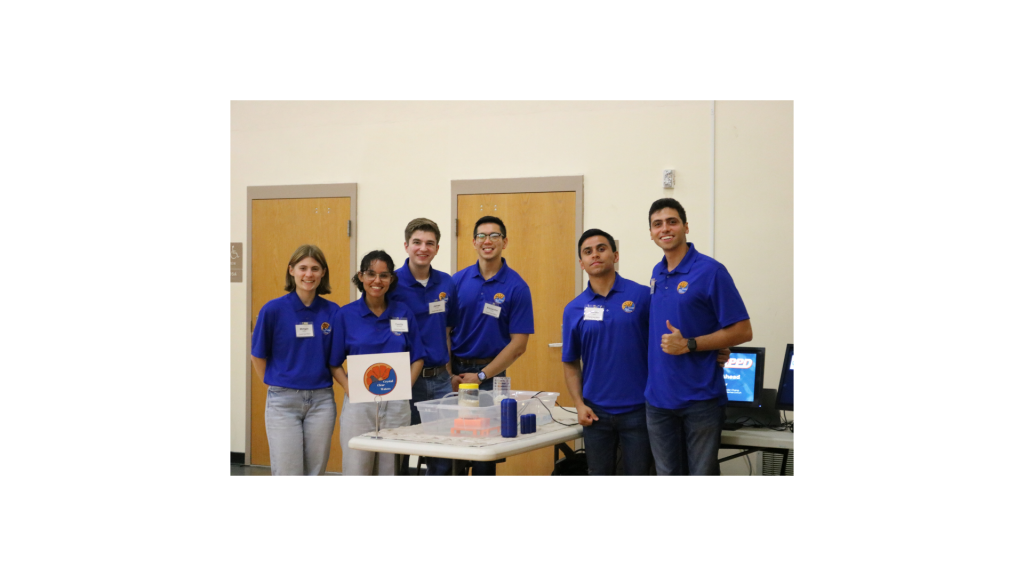