
3D Printing or additive manufacturing is an emerging manufacturing method that allows people to create complex structures and features previously impossible to create with other methods. Essentially, a thermoplastic material gets pushed through a hot extruder and is deposited onto a flat bed. As the thermoplastic is extruded through the hot-end, it melts to a stringy, almost liquid state. When it contacts the bed and the hot-end moves away from it, the plastic rapidly cools and becomes a solid – similar to how a hot glue gun works, except this one is attached to a robot. The hot-end moves in the x, y, and z directions to make a part based on the inputted design from the user.
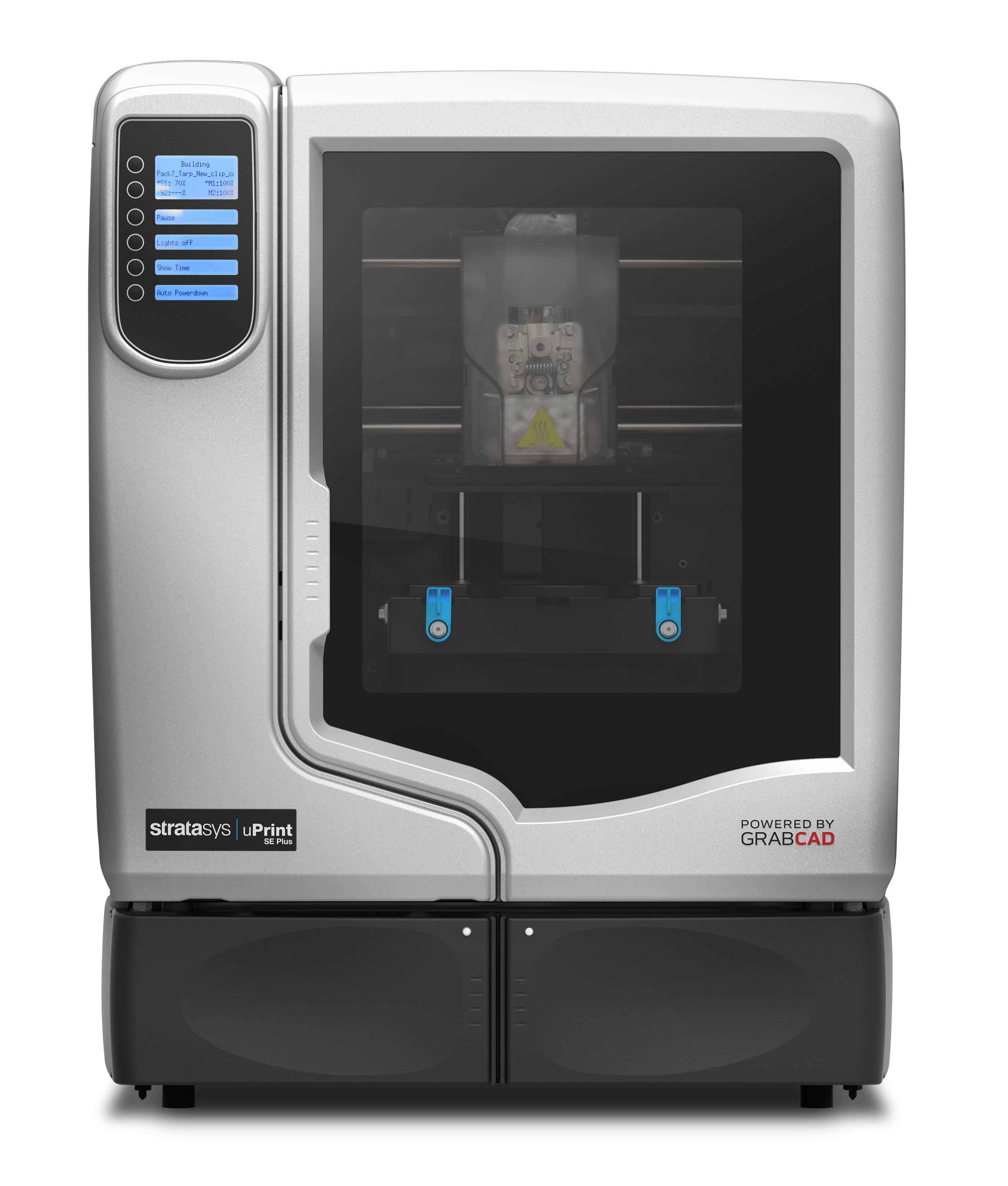
We are using 3D printing extensively in our project to rapidly iterate and prototype. We can use one variation of a design one week and have another design ready for the next week. Whereas if we were to manufacture it traditionally, the lead time between prototypes would be extensively increased. We use 3D printing mostly in our autonomous charging prototype since it is undergoing the most iterations. However, we are also integrating 3D printing into other subassemblies of our project to reduce manufacturing times and to create more complex designs.