Final. Design. Review. The three words at the back of our minds for the past 9 months. The culmination of two semesters of meticulous designing, prototyping, and development. The DesiGators knew the stakes were high and were ready to put on a show, and that we did! The team had the amazing opportunity to present their completed dehydrator to all of the IPPD teams, their coaches, and liaisons present at the FDR event and it went flawlessly. This was the first opportunity the team had to present their project to the majority of the teams within IPPD, so it was also many of their first times seeing our design.
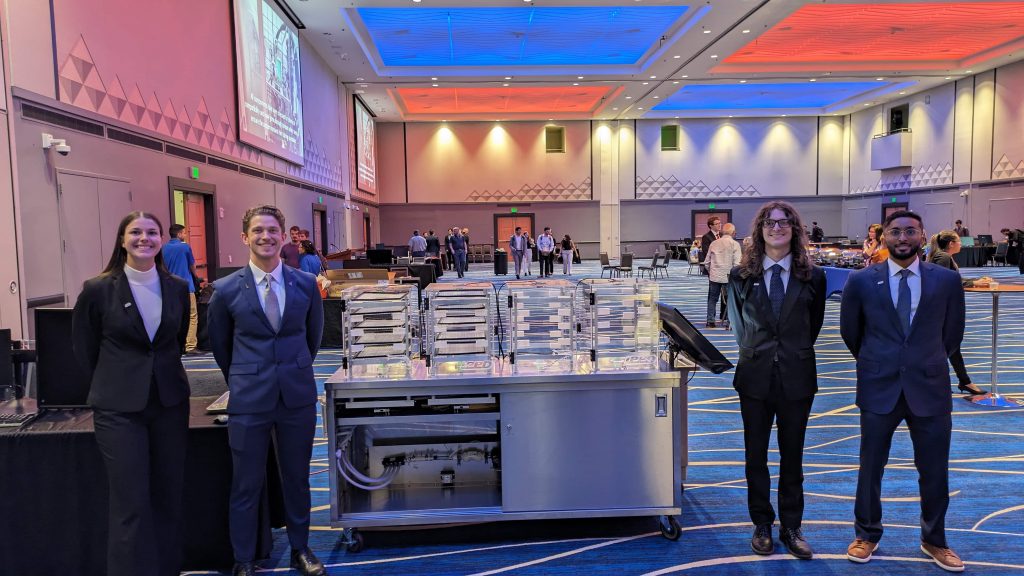
The project unveiling drew many awestruck gasps from the crowd but also interest during the part of the program open to the public. The team fielded questions from several interested parties who wanted to learn more about the design and how it could be used as a teaching tool.
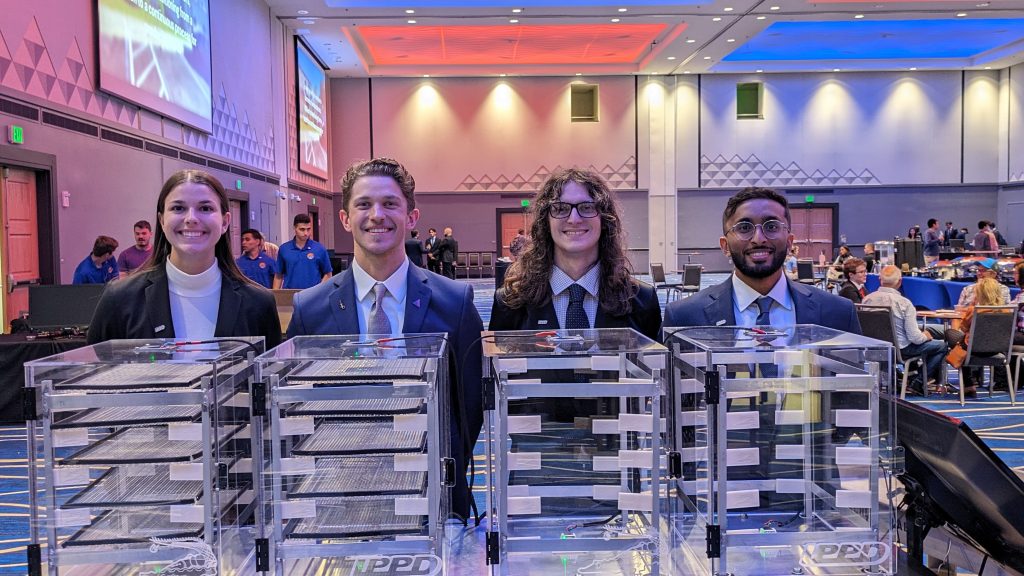
And that’s it! The DesiGators are done. Kaput. Sayonara. It was a good run while it lasted….SIKE. The DesiGators have one last hurrah left in them as they will be attending the Capstone Conference this June. Stay tuned for more blog posts and a DesiGators reunion this summer!
See below the poster that we will be presenting at the conference as well as a promotional video for our dehydrator – with a breathtaking Blender animation made by the DesiGators’ own Korynn Haetten! View the video at the link below: https://youtu.be/qUwGS8T2424
Also, here’s a sneak peek at the poster the DesiGators will be using at the conference this June!
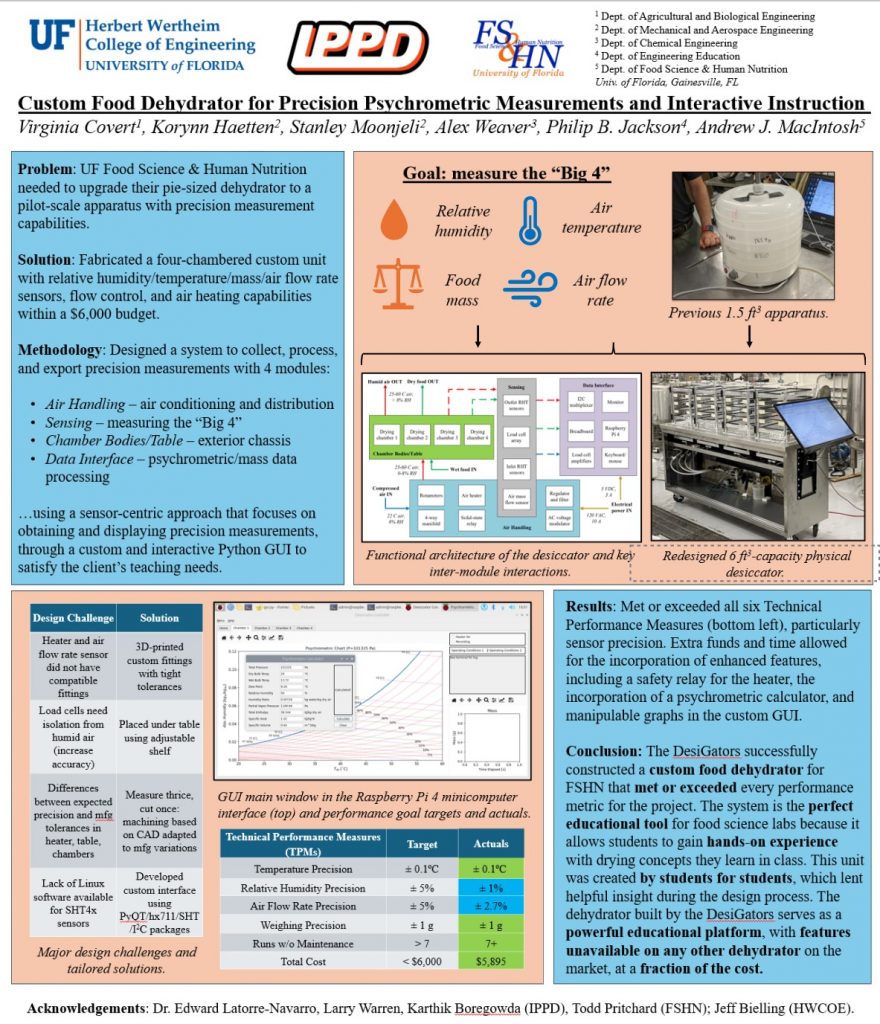