The DesiGators weeks of hard work have finally paid off! The team now has all of the necessary components needed to begin another (almost) fully integrated drying run. Apple slices were used in this iteration of the testing phase and placed on the completed drying racks atop the load cells. The relative humidity and temperature sensors were attached to the drying chamber and the unit was left to run for 24 hours. The team was able to collect data successfully over the 24 hour time period and dried the fruits completely! The second drying test was a success!
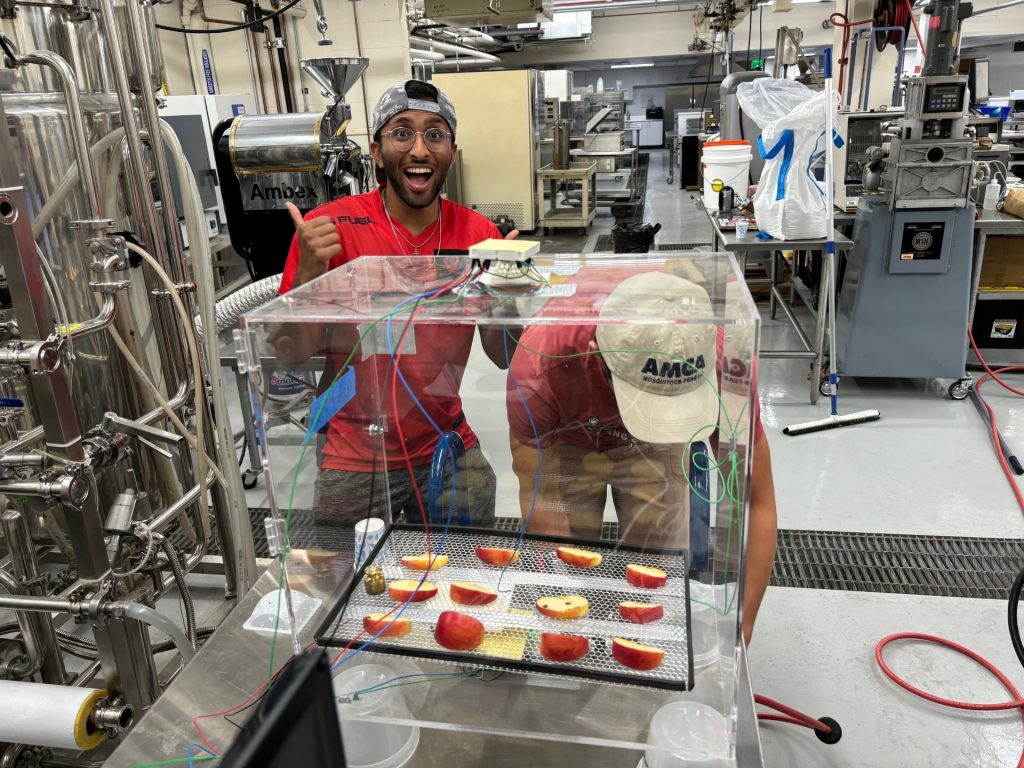
The team spent this week assembling all the metal parts needed for the load cell subassembly. These parts have been sent to the FSHN technician to get welded for the final assembly. A model of the final welded assembly is shown below.
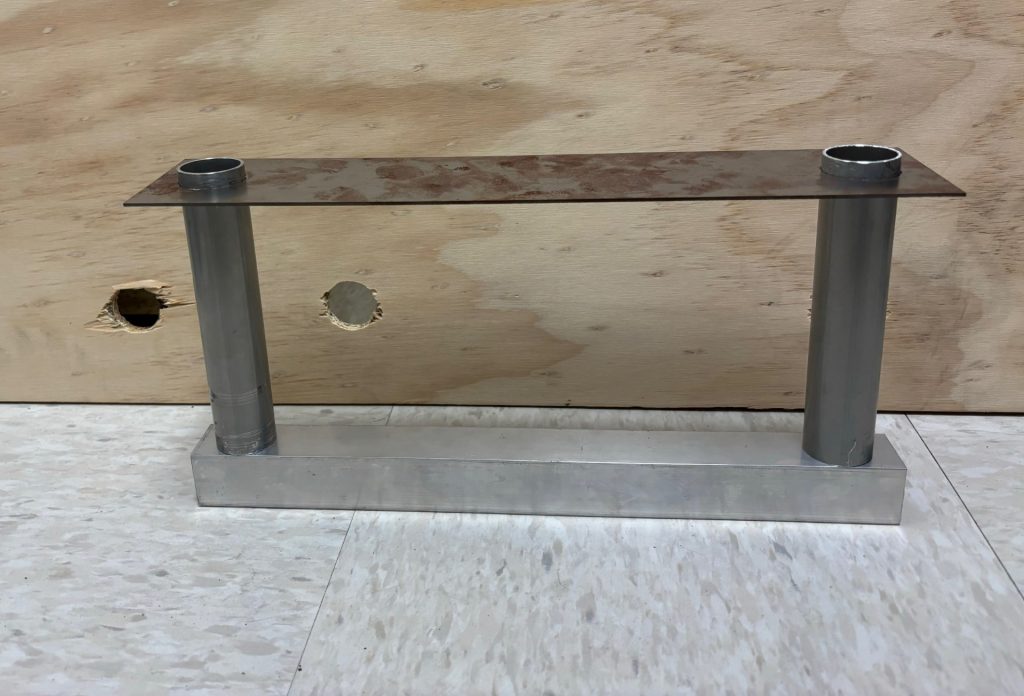
The team also sent over the metal support material so that a test version of the shelving assembly could be welded and placed within the chamber. Once the team verifies that the shelving assembly will fit neatly into the holes in the drying chamber they will be able to produce final versions for all four chambers.
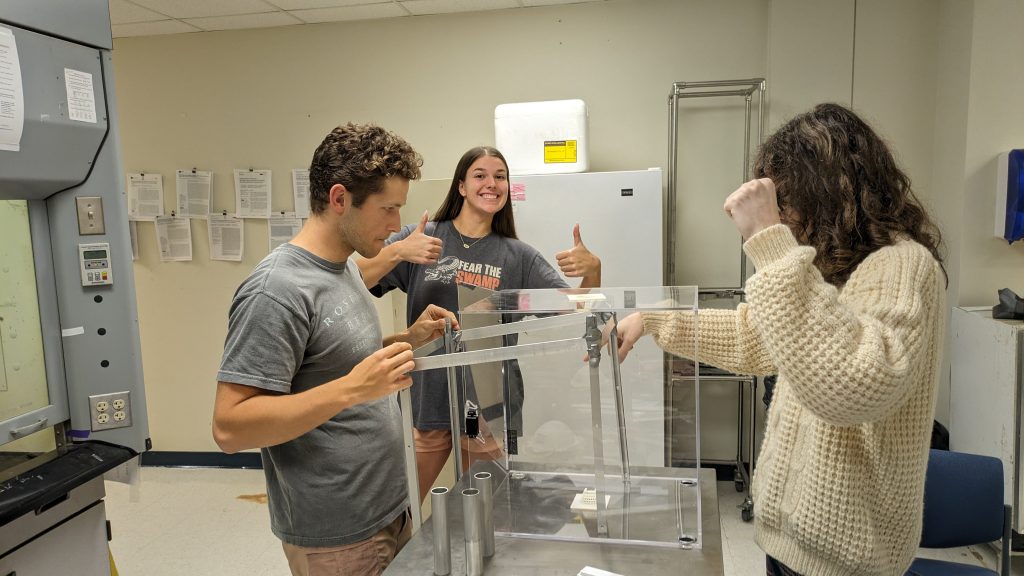
The team did run into a bit of a roadblock this week in regards with the heater ordered from Tutco-Farnam. The team believes that the heater that was delivered did not match what was ordered. The team wanted NPT fittings on both ends of the heater and the heater that was delivered did not have that. The team believes that this is an error on the manufacturer’s end and hopes to work with Tutco-Farnam to resolve the situation amicably.
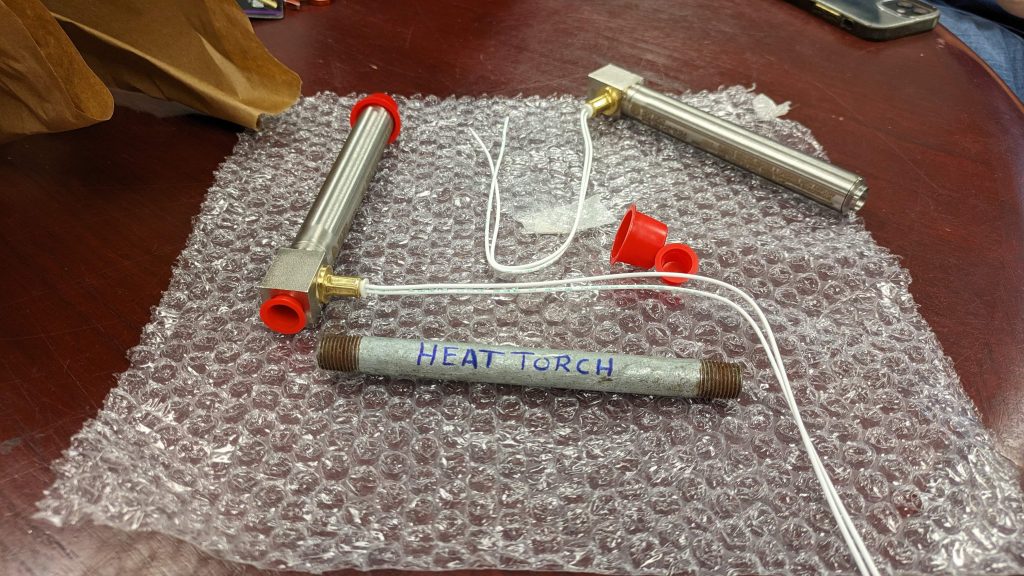