The FSHN lab was a buzz of drilling, coding, filing, cutting, and assembling this week as the DesiGators continued working hard on both the manufacturing and software fronts. The team assembled the air handling subsystem in its entirety, with the exception of the heating element which is still being prepared by the manufacturer.
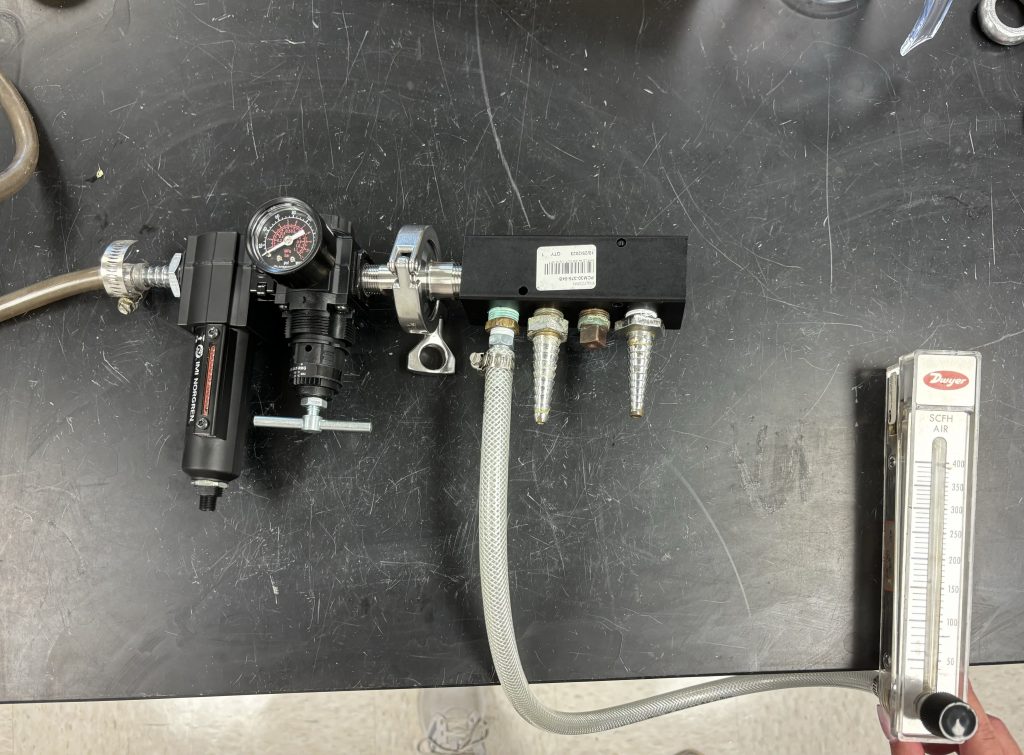
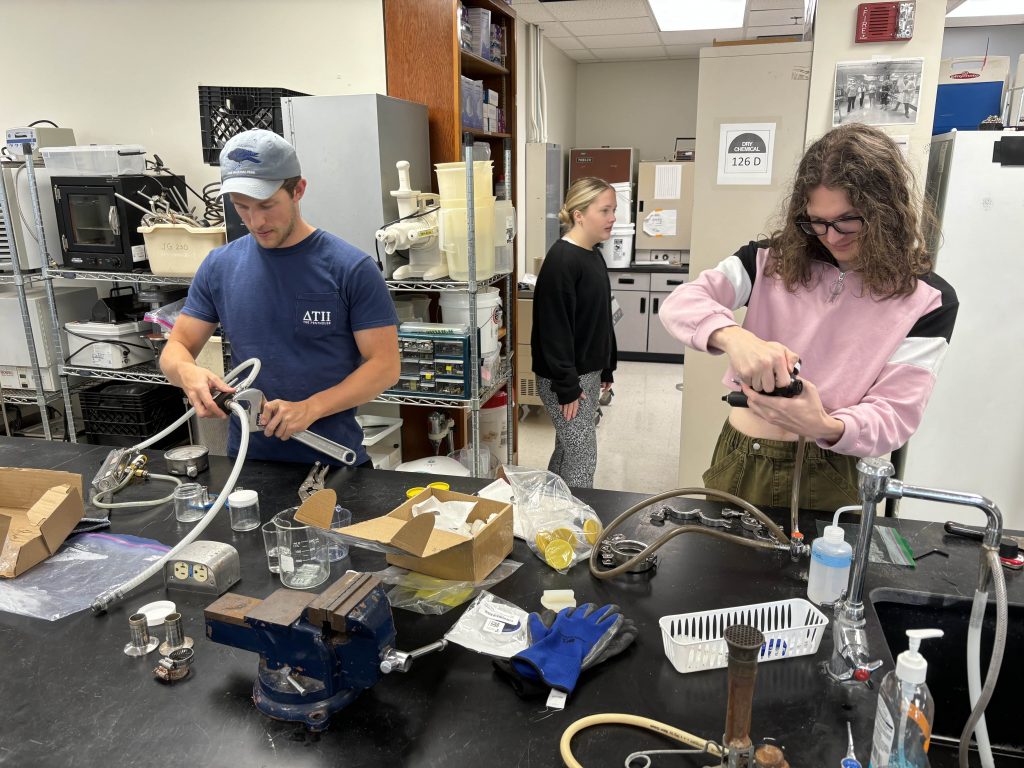
The team also received the rubber tubing that will be used as a safeguard against the sharp edges of the metal drying trays. The team spent hours cutting the tubing to size and gluing it securely to the edges of the chamber, and now has over 20 finished trays – that is the first part of the assembly that is one hundred percent complete!
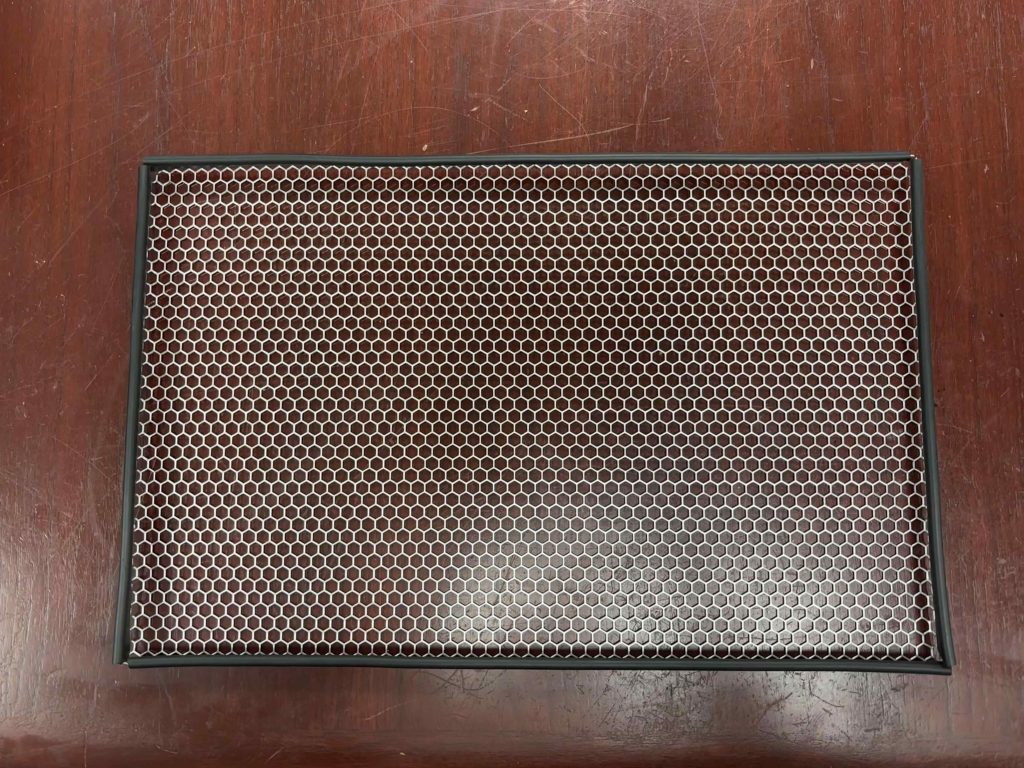
The team also talked with FSHN technician, Todd Pritchard, on the best way to assemble the metal components for the dehydrator since they will require precision welding. The team determined that the best idea would be to order all of the metal parts needed, create a test build of the needed components, and then weld everything all at once to be as precise a fit as possible. A mockup of the metal assembly that will be used to combine the load cells and the shelving materials is shown below.
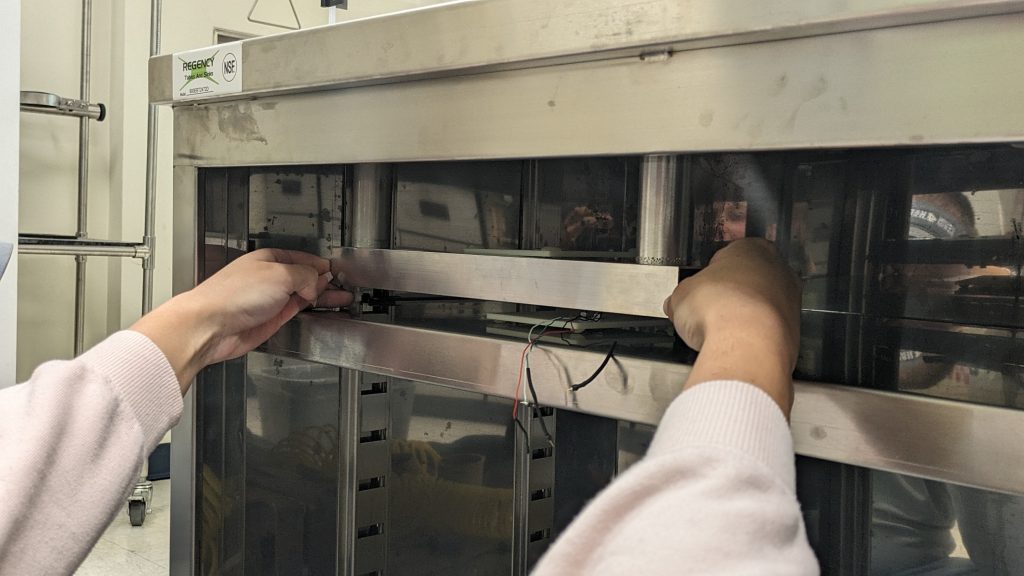
With all the hard work going around, the DesiGators have made sure to keep morale high and enjoy themselves throughout the project. Enjoy the pictures below of the team sharing meals and making the most of their time in the lab!
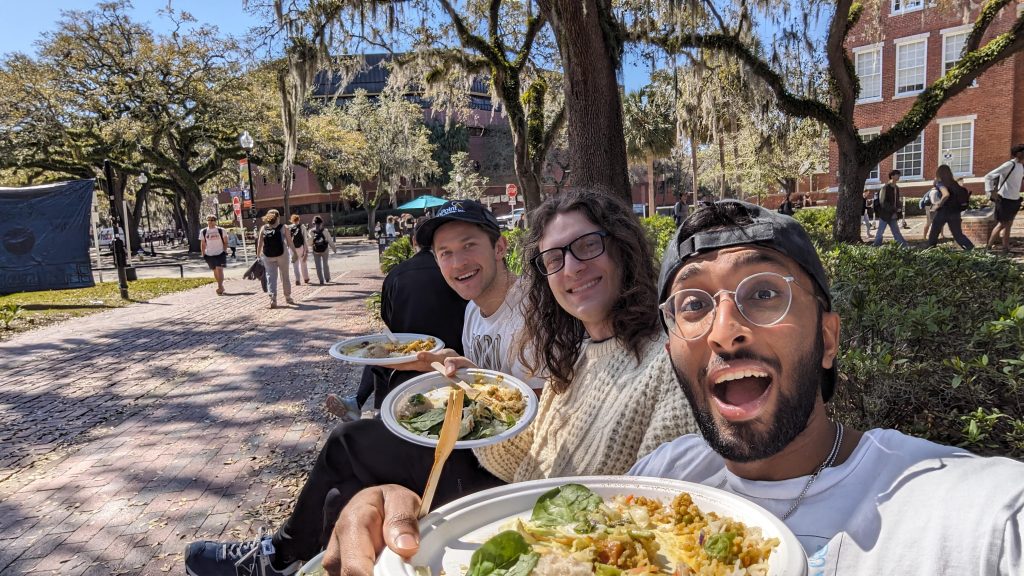
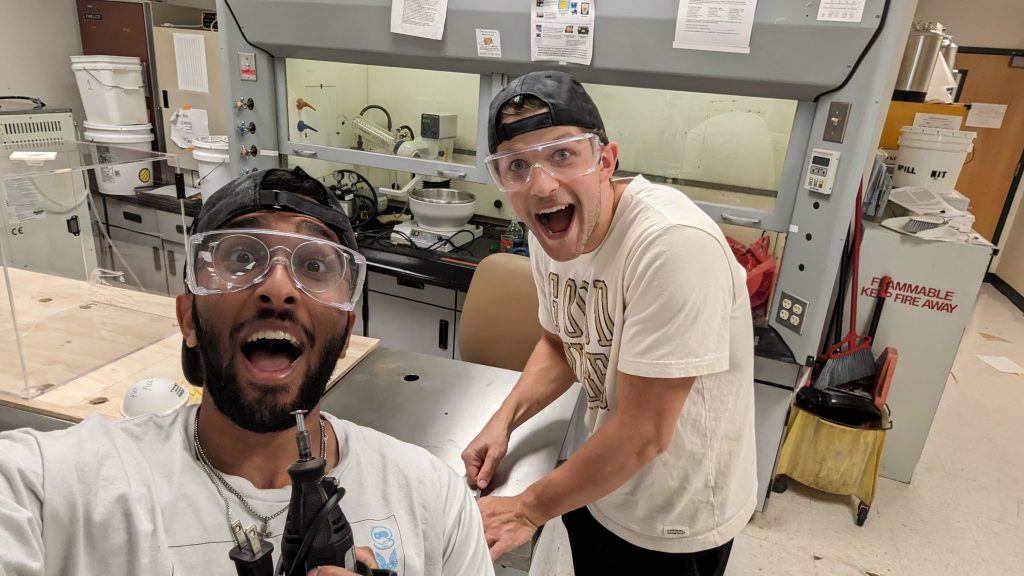