Don’t worry, we didn’t work during all of UF’s official spring break! But that doesn’t mean Parrotronix was slacking off either. A huge part of our progress over the last two weeks has been preparing as many components for manufacturing ahead of our team’s full return to campus after the break. This includes our motors, mounting blocks, fasteners, and the largest subsystem of the animated figures themselves: Their shells!
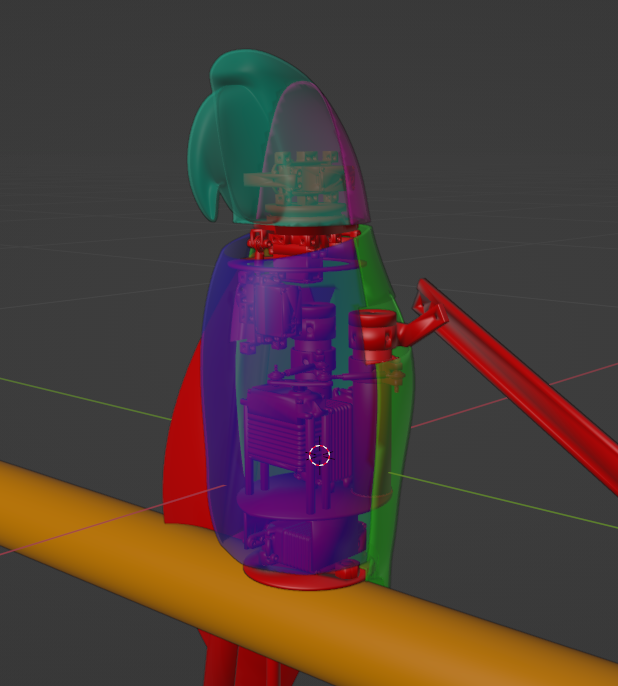
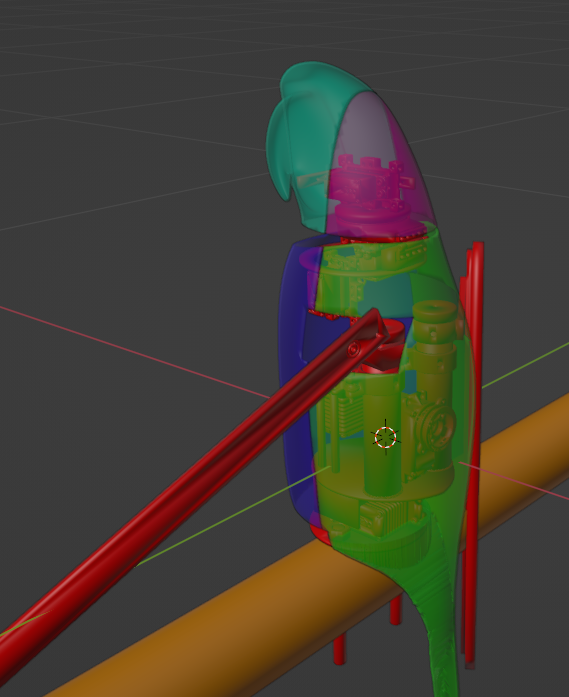
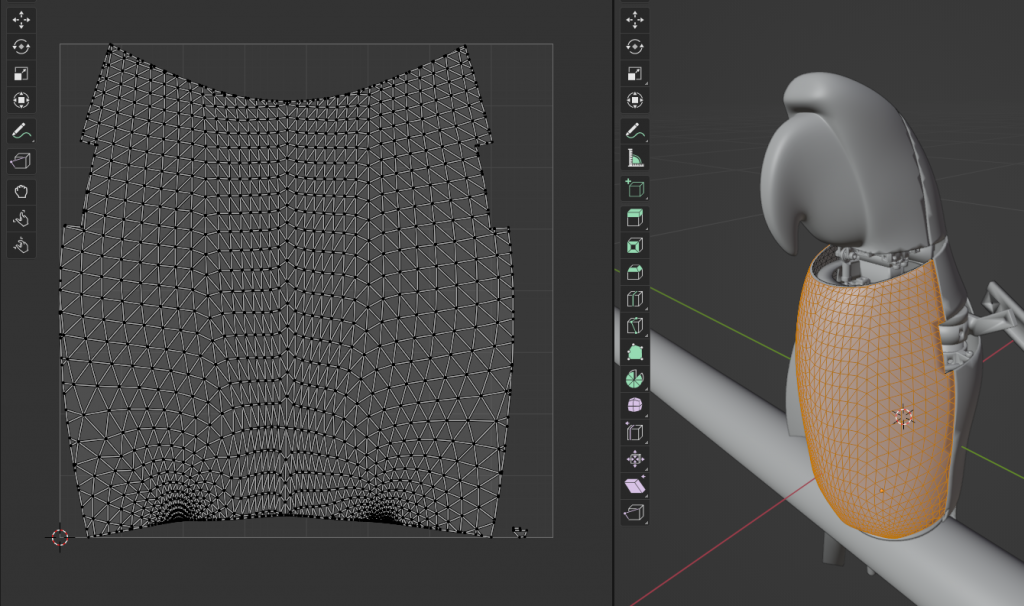
Now, parrots don’t usually have shells, but they also aren’t usually filled with wiring, linkages, and servo motors! In order to create a cohesive look for each of our figures, we took time over break to do some Spring Cleaning of our 3D models, including digitally sculpting our birds. Our team has been working in Blender, an extremely powerful and free 3D mesh software that is widely used in the entertainment industry. Using the sculpting and mesh editing tools, we can artistically shape our birds while ensuring all of the critical mechanical systems are contained properly. This is also the step where we add cuts to allow for the large range of motion in the figure, as well as mechanical connections to the skeleton of each figure. Once these parts are printed, our scenic team will follow up by preparing a fabric pattern for each section, with help from some of Blender’s built in texturing tools.