The PolarFlow Optics team recently reached a significant milestone in their journey – the Final Design Review on Tuesday, April 23rd. This momentous occasion marked the culmination of two semesters of dedicated work and collaboration.
In attendance were our esteemed liaison engineers from Johnson & Johnson Vision, who have been integral partners throughout this process. With anticipation and pride, the team presented a comprehensive overview of all that had been accomplished, showcasing the evolution of our project from concept to reality.
One of the highlights of the presentation was the display of 3D printed iterations of our prototype, providing a tangible representation of the progress made. Alongside this, the final prototype itself stood as a testament to the team’s innovation and perseverance.
Crucially, the testing results from the Netherlands facility provided concrete evidence of the effectiveness and reliability of our solution. This data served to validate our efforts and reinforce the confidence in our design.
As the presentation drew to a close, the team compiled all their hard work, insights, and recommendations into a comprehensive final report. This document not only encapsulates the journey of PolarFlow Optics but also serves as a roadmap for future endeavors in the field of optics and innovation.
However, it wasn’t all about work – the team seized the opportunity to celebrate their achievements and foster camaraderie with a well-deserved team bonding activity. What better way to unwind and reflect on a successful year than indulging in some delicious Tuesday Tacos at Cantina?
The Final Design Review wasn’t just a conclusion; it was a celebration of collaboration, dedication, and ingenuity. As the PolarFlow Optics team looks towards the future, they do so with a sense of accomplishment and excitement for what lies ahead.
Below, you can see a picture of our team after FDR!
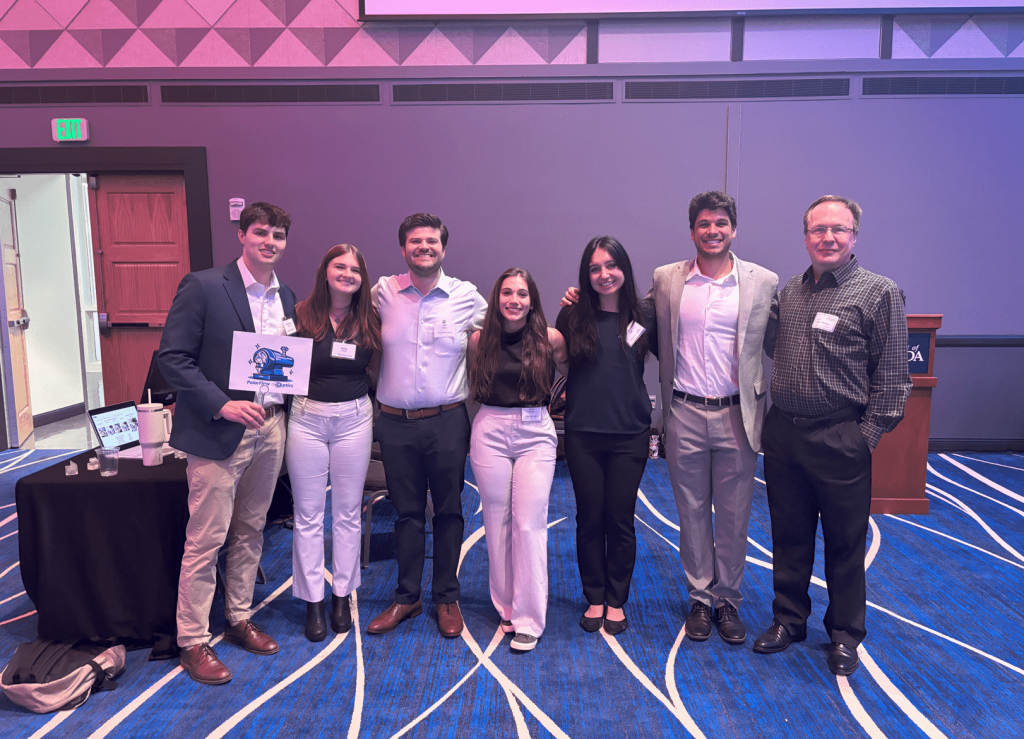
Figure 1: picture of PolarFlow Optics team with their coach, Dr. Butler
Promotional video:
https://youtu.be/HivtrQrrcQM
Poster:
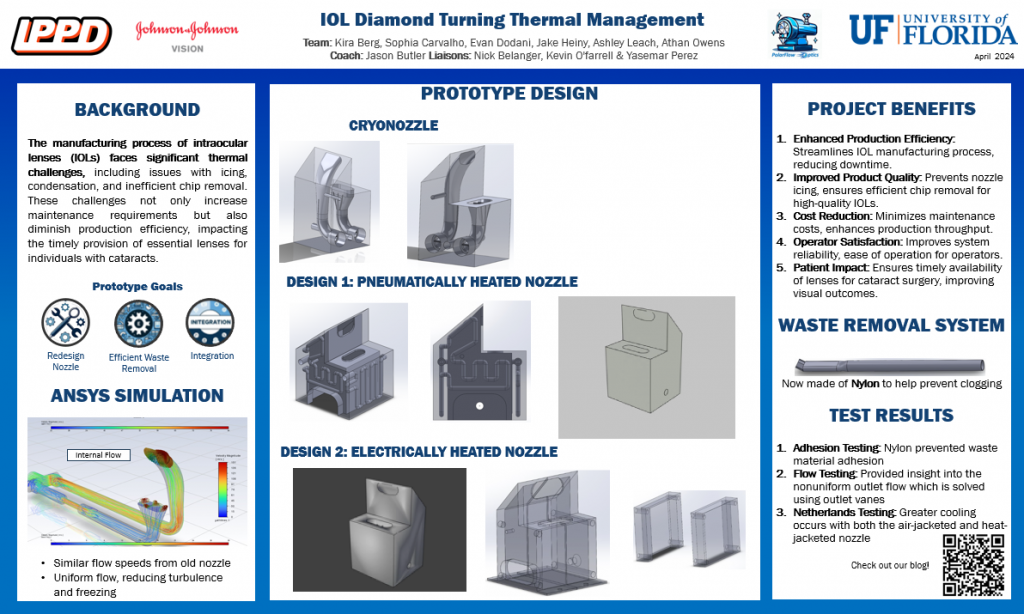