This week, the Road Watch Team had its first in-class work session. These are a new feature of IPPD 2 that were not offered in IPPD 1, as IPPD 2 focuses primarily on the practical realization of the system (which necessitates collaborative in-person work). It was very nice to have all team members physically together in one place, all working on different parts of the system. This provided a good opportunity to quickly exchange ideas between teammates and to catch up on everyone’s progress. Director Latorre indicated that these in-class work sessions would be a bi-weekly occurrence, which is greatly appreciated by the Road Watch Team. Currently, work is distributed between teammates as follows. Darrion is developing the LiDAR driver for the Jetson Nano. Evan is working on identifying predictive machine learning algorithms. Will is evaluating the camera throughput on the Jetson Nano. Rolando is identifying an IMU to assist in aligning the system. Skyler is designing the system enclosure. Finally, Billy is identifying power supplies for the system. Be sure to follow future posts to see how each group member progresses in their tasks.
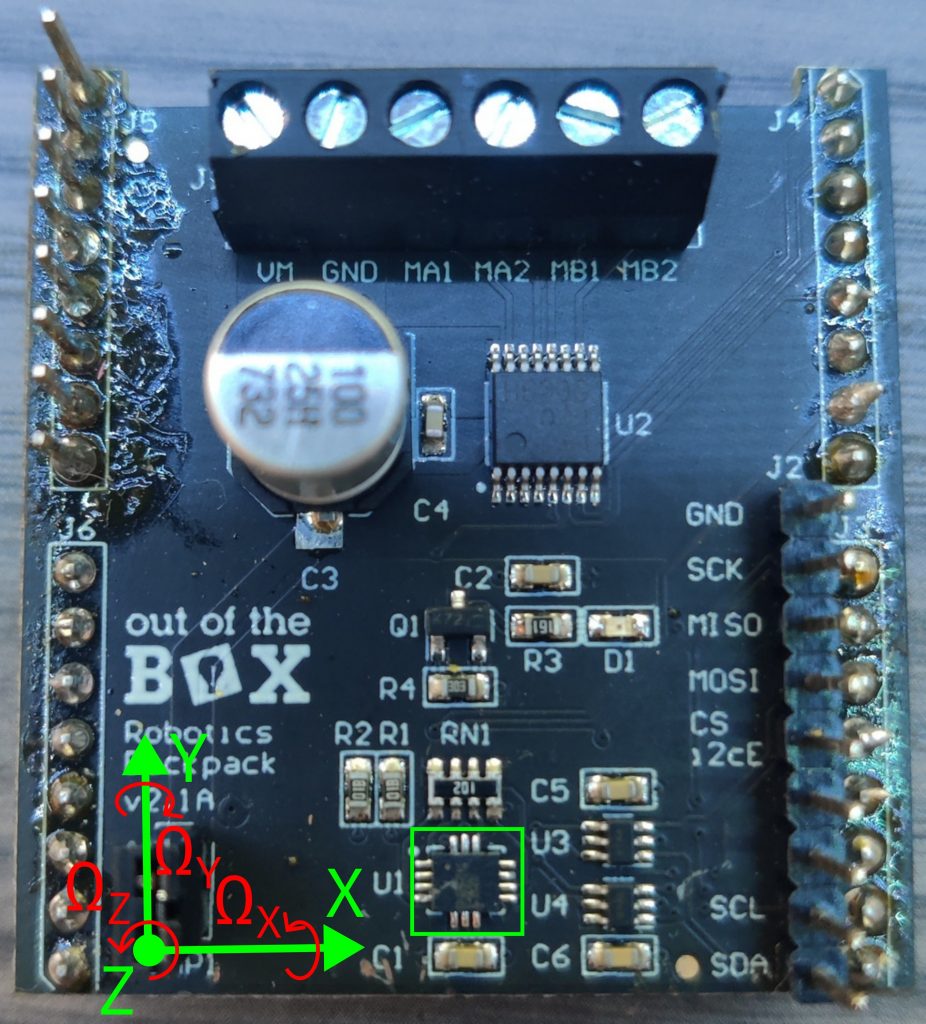