Our team put in some serious lab time this week, and it has paid off! We reached some big milestones and have stayed on track with our project plan. The software team was able to connect the Raspberry Pi to the touchscreen display and download files to it. The mechanical team used this advancement to refine the design of the housing that holds the touchscreen and create holes to mount it to the doorframe constructed last week. The RFID team is able to read the tag data from the reader and has begun working on sending it to the microcontroller. This will merge with the efforts of the microcontroller team, who has been working on UART communication and has the Pico functioning with one of the ultrasonic sensors.
This is great progress for the system’s sub-components, and as we head into next week, our sub-teams will start to merge as we begin to integrate. Successful integration is key for having the most accurate system possible, so we are eager to get to work!
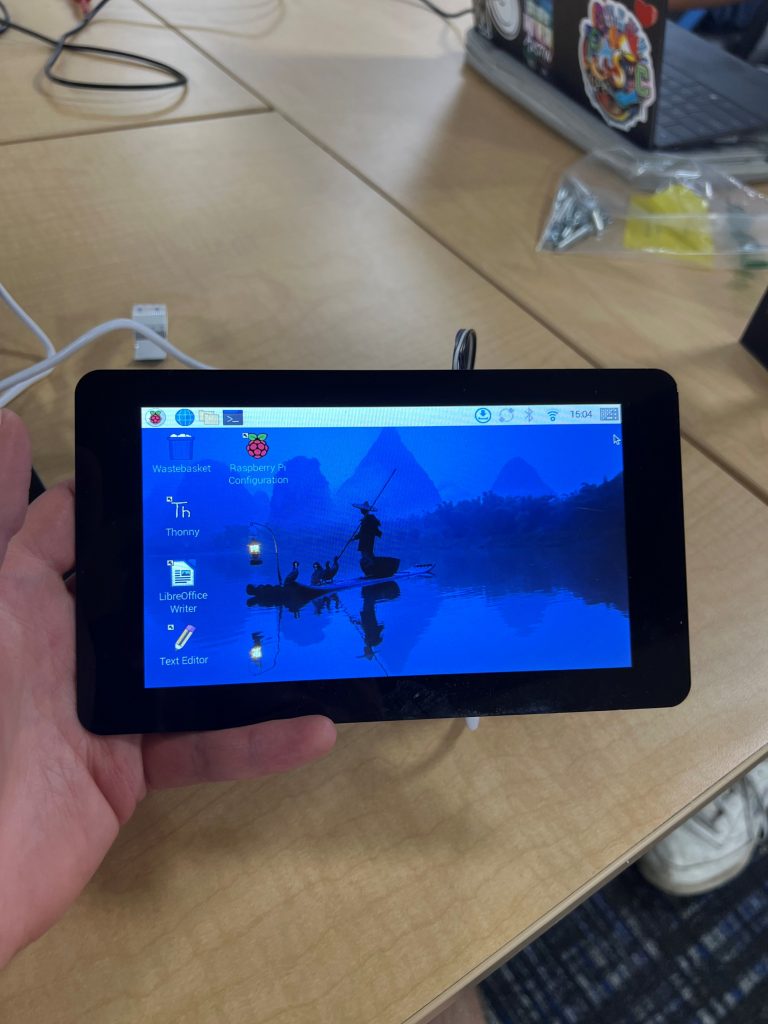
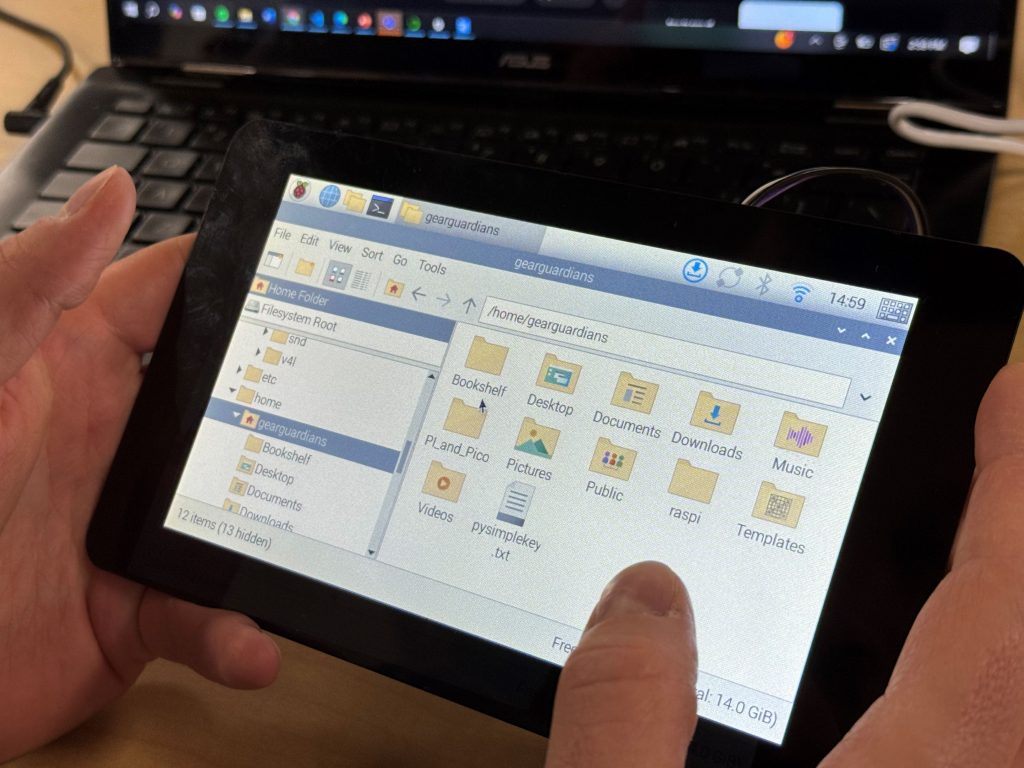