Our team is deep in the preparations for PID! We are super excited to share what we have been working on with the judges.
Our ChemE team has been diligently working towards making a skeleton of the Aspen Simulation for testing purposes. They believe that they will be able to successfully recreate the existing process within Aspen Plus.
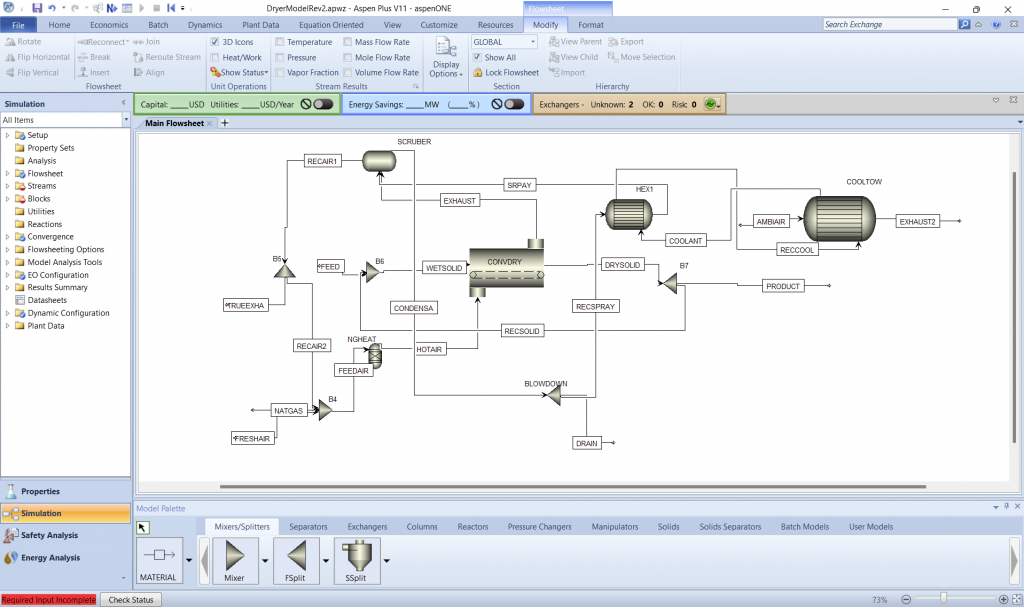
Our MechE team has been actively working to make an Ansys Fluent simulation of a single drying chamber to accurately model the heat transfer inside any of the drying chambers.
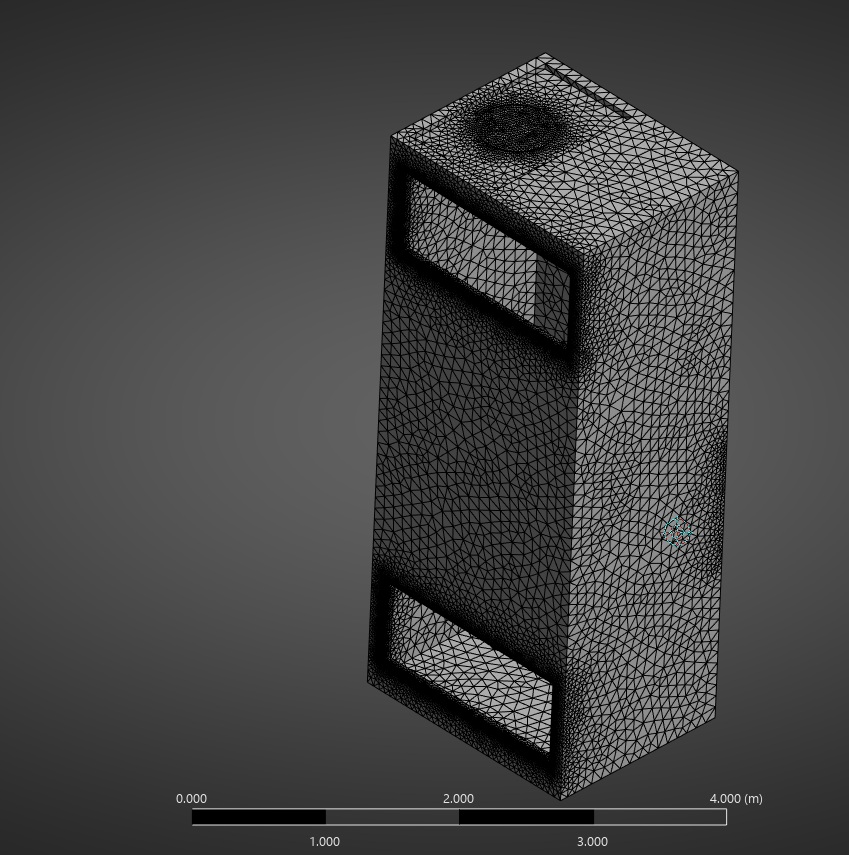
Our feedstock team has been working towards writing the experimental plans for all the tests necessary to run both simulations, such as creating a particle size distribution and getting the heat capacity of the wet product.