While we were investigating which process simulation software to use for our project, one of the options we were investigating was called SuperPro Designer by Intelligen [1]. This made it towards the top of the list because one of its listed features is that it has the capability to model a convective dryer. Below is an example of SuperPro Designer’s capability to simulate process equipment!
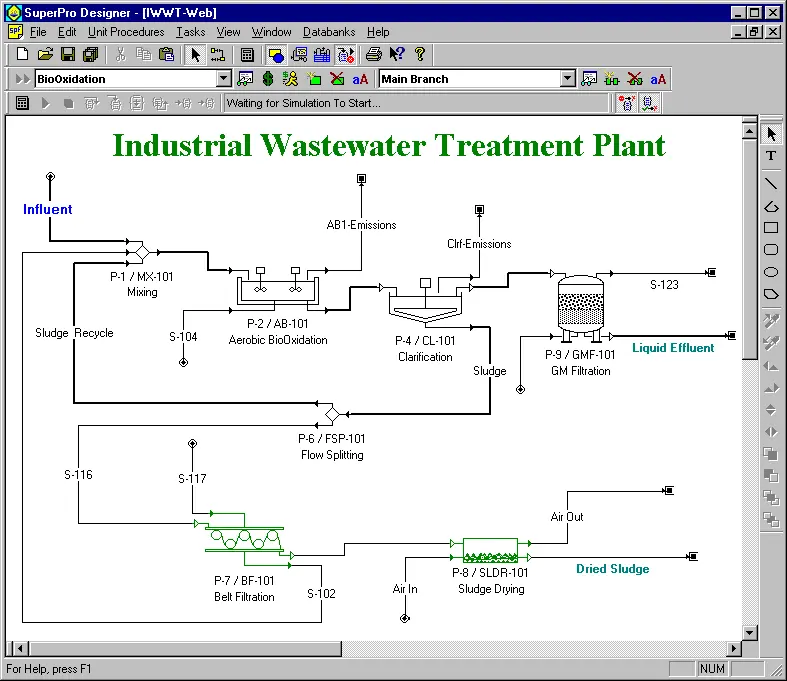
From the above example simulaton, we can tell that SuperPro has many similar features to Aspen Plus. Both simulators are capable of handling reaction thermodynamics, they are both capable of handling solids feed and product streams, they can both even handle convective drying! Ultimately, we ended up choosing to use Aspen Plus because all members of our ChemE team have the ability to access it, while we only have very limited access to SuperPro Designer.
Relationships:
[1] Intelligen, Inc., “SuperPro Designer Product Features,” Intelligen, SuperPro Designer, SchedulePro, EnviroPro, https://www.intelligen.com/products/superpro-product-features/ (accessed Feb. 20, 2025).
[2] Intelligen, Inc., “Wastewater Treatment and Pollution Control,” Intelligen, SuperPro Designer, SchedulePro, EnviroPro, https://www.intelligen.com/industries/wastewater-treatment/ (accessed Feb. 21, 2025).