We would like to share our final poster and video here for those who were unable to attend the FDR event or want to review the work we completed.
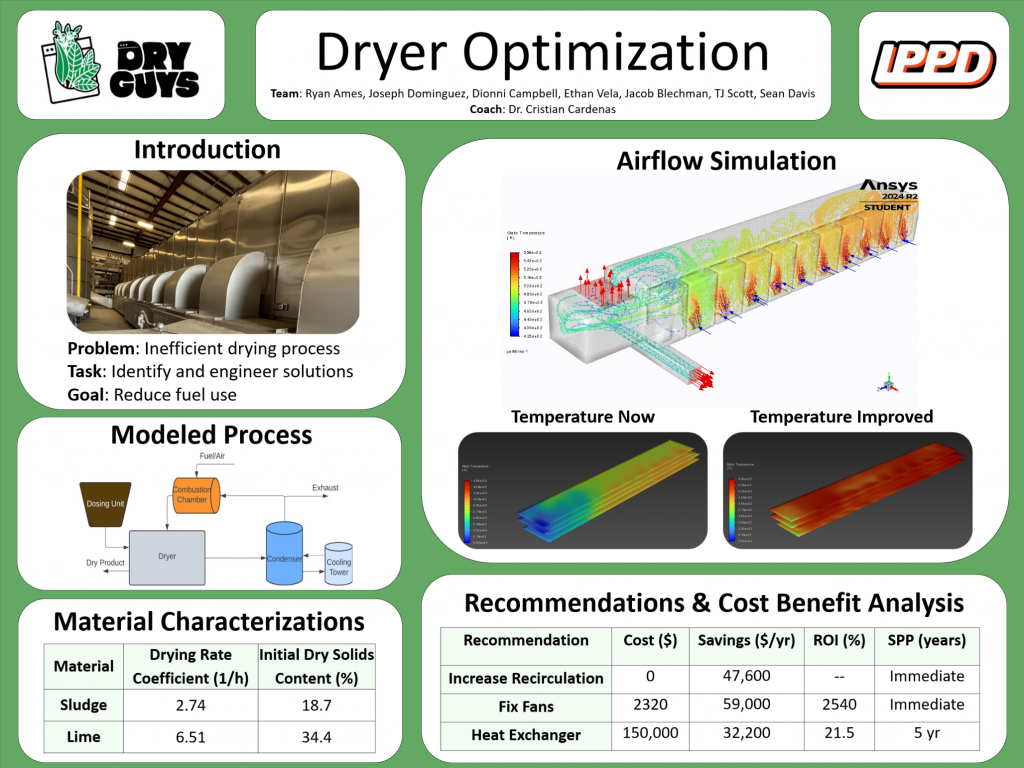
We would like to share our final poster and video here for those who were unable to attend the FDR event or want to review the work we completed.
It has been 2 busy, exhausting, and enlightening semesters that the Dry Guys have journeyed together. We are excited to say that we have successfully completed our Final Design Review. We were able to bring real improvements to our sponsors process that will both save money and make money. While this leg of our career journeys is over, we are excited to see where we will all go next. Thank you to our sponsor for an excellent project that pushed us to learn new things and thank you to the IPPD staff for supporting us along this journey and providing us with all the necessary resources to get here and thank you to everyone who stopped by during the IPPD public showcase yesterday to check out our project!
This week, Dry Guys was hard at work in preparation for FDR on the upcoming Tuesday! We really appreciate all the recommendations that our fellow IPPDers gave to us during Peer Reviews this past Tuesday, they were all really helpful. Pictured bellow is Dry Guys doing a practice run of their new and improved FDR presentation! We are so excited to give this presentation to our sponsor and to show off all the work we have been doing all semester. Good luck to all the other teams with their presentations!
With FDR approaching rapidly, we wanted to do one last site visit before it became too late. During this site visit, we wanted to focus on doing an experimental run that would provide us with results that would prove one of our recommendations to our sponsor rather than just relying on our simulations. While the simulations are a very good tool for characterizing a system, nothing speaks louder in a presentation than real-world results. With these real-world results, we can also establish any real improvements that were made and present them to our sponsor, which is another piece of an engineering presentation that speaks louder than words or theories. We are excited for what these results will be able to add to our FDR presentation!
Also, our team was selected to give a special presentation that would serve as an additional test run for FDR! We had an excellent presentation, and we want to thank the IPPD team for inviting us out to it.
This week, Dry Guys participated in the second Prototype Inspection Day event! We were so excited to present on our prototypes and the results that we have drawn from them, and we are very thankful to all of the judges who participated in this event to provide us with feedback.
We received some excellent feedback and suggestions from our judges. One major piece of feedback was we should a more complete benefit with numbers to all of our equipment recommendations to make it more clear to the audience why they are being recommended. Another great piece of feedback we received was to be clearer about the testing plan that we used to get to our recommendation. And as always, make sure to keep your hands out of your pockets and your arms uncrossed!
This week, the Dry Guys took some time to make a site visit to our sponsor to double check some of our assumptions about their process. The most important assumptions we were confirming were the airflow patterns inside the dryer and some of the dimensions of the inlet ductwork that we assumed were even. During this investigation, we discovered that some of our assumptions were incorrect, making this a very important site visit in preparation for PID and FDR. Correcting these will make our results much more accurate to real life!
References:
[1] B. Corabel, “Easter Spring Break 2024 USA – Brynn Corabel,” Brynn Corabel – Explore ideas, tips guide and info Brynn Corabel, https://rosalinewcybil.pages.dev/uncnqoe-easter-spring-break-2024-usa-nrentnn/ (accessed Mar. 12, 2025).
Our CFD is excited to share some important findings that they discovered while simulating various test cases of the dryer. Without sharing anything too specific, we will discuss a series of different images from 3 different test cases here. Image 1 below will be the first test case with low recirculation flow and regular mass flow inside the dryer.
From Image 1, we can see that the lines – which represent airflow paths – are fairly well distributed inside the dryer. This means that the dryer has an even distribution of air inside that is making contact with the feedstock. Next, we will investigate design recirculation and normal mass flow in Image 2.
From this test case, we can see that a hole has appeared in the middle of the dryer where no air flow paths reach. This is significant because we can now draw the conclusion that increasing the speed of the recirculation fans pulls air away from the middle of the dryer. Finally, we will investigate one last test case with high recirculation and normal mass flow in Image 3.
In this test case, we can now see that the hole in the center of the dryer has become more exaggerated and at this point it is likely impacting the mass and energy transfer between the air and the feedstock because it is reducing the overall surface contact between the two materials. This is significant because this impacts the overall performance of the dryer and the quality of the final product. We can now confidently say that increasing recirculation pulls air away from the center of the dryer and impacts the performance of the dryer. We also believe that the overall mass flow rate of air is important and may also impact the performance of the dryer, so will be testing that in the weeks to come!
This week the Dry Guys have been hard at work improving our simulations!
A little sneak peek from our CFD team is that they were able to significantly reduce the amount of error in many of the pieces of their simulation. This will greatly improve the confidence of our engineering recommendations for Green Technologies.
Our Feedstock Teams has nearly completed all of their tasks. They have already submitted all of our samples for analysis at the Geological Sciences Department, and we have gotten some of the results back. The only major thing left is to normalize the drying curves so that they can be input into Aspen.
The ChemE team was able to get all the separate sub-system simulations to converge this week so they can begin working on the whole system simulation. The major breakthrough that they made this week was converging the dryer sub-system simulation. The trick to getting this simulation to converge was to separate the dryer into its individual compartments. This more accurately simulates what is occurring within the equipment, and this leads to a more accurate solution.
This week, we want to take a second to showcase some of the work that our Feedstock team has been working on.
First, one of the major necessary tests to get the Aspen model to converge was the particle size distribution (PSD) test. This test is done on the dry product to determine the amount of different sized particles present in the feedstock. This is important because smaller particles will dry faster than larger ones. This test is conducted using sieves that separate the particles into a number of intervals that will input into Aspen as PSD data.
For the thermodynamic characterization of our feedstock, the team has chosen to utilize UF’s department of Geological Sciences to help us complete the many tests that need to be conducted. The Geological Sciences department at UF is capable of conducting all of the tests that are required for our ultimate analysis of the feedstock. This includes the characterization of carbon, hydrogen, sulfur, nitrogen, and oxygen [2]. This is done using a tool called mass spectroscopy.
References:
[1] J. Fuentes, “Understanding everything that is particle size distribution (PSD),” Engineeringness, https://engineeringness.com/understanding-particle-size-distribution-psd-importance-measurement-techniques-and-applications/ (accessed Feb. 26, 2025).
[2] “Stable isotope mass spectrometry facility,” UF Geological Sciences, https://geology.ufl.edu/research-and-facilities/facilities/stable-isotope-mass-spectrometry-facility/ (accessed Feb. 26, 2025).