With time barreling toward the upcoming FDR presentation, the team was able to close much of the distance to the finish line this week. Upon receipt of a new stepper peristaltic pump, the electrical sub-team rushed to integrate it into the team’s project. They successfully did so, calming worries about not having a powerful enough motor for the system to work. On another great note, the team’s second iteration of resin 3D printed sleeves was even better than that of last week. Sadly, the team’s Raspberry Pi gave out, so a replacement will need to be purchased.
Stepper Motor Pump
The electrical sub-team has programed a new peristaltic pump, which can reach even higher flow rates than the previous two pumps. Due to the motor in the pump being a stepper motor, as opposed to a DC motor, the electrical sub-team was able to wire it perfectly to fit within our electrical system. The untimely death of our Raspberry Pi means that our electrical system will have to wait until at least next week to be complete, however.
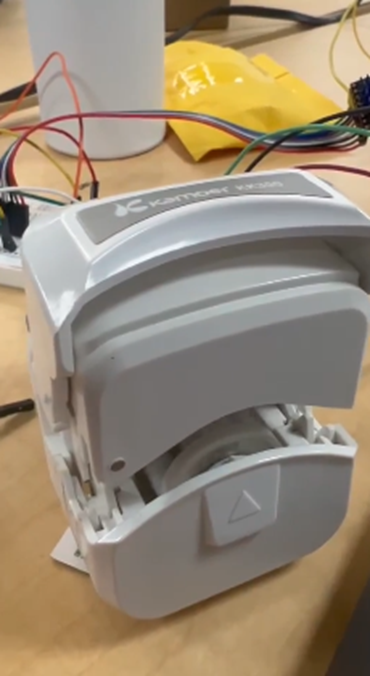
Flow Rate Remote
As far as the flow rate remote goes, the team has created a new attachment that allows the remote to fit onto a cylindrical shaft. Smaller pieces of the cylindrical attachment were sent to print to test sizing onto a pre-existing shaft that the team uses. If the fit is perfect, the team will print the full remote-shaft attachment.
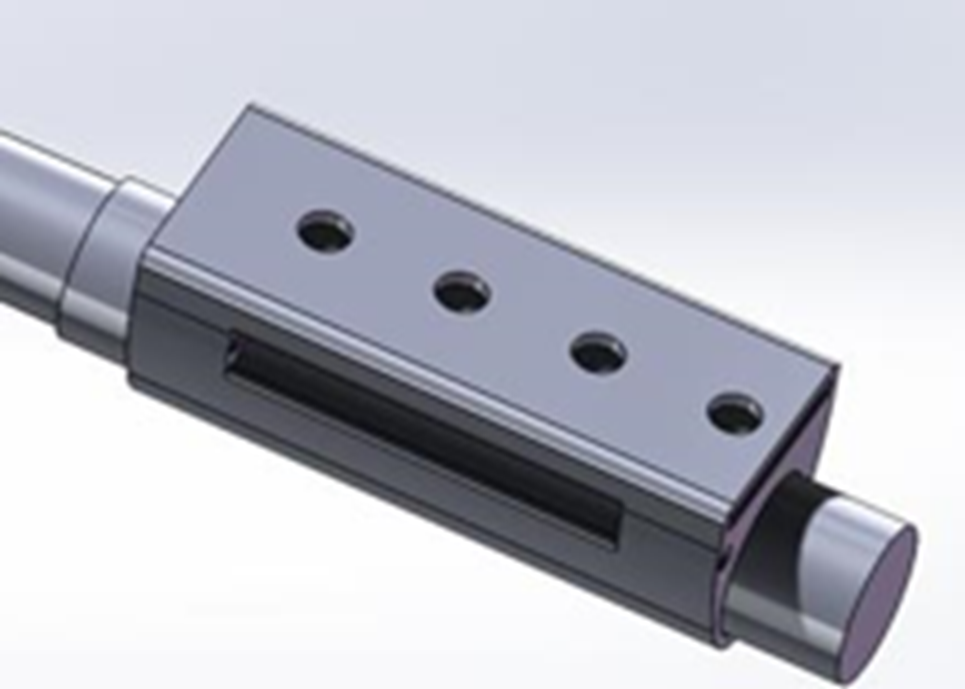
Tube Attachment Prints
The team received eight new resin printed sleeves from David Sante. Testing the flow of water through the sleeve as well as the amount of coverage at the tip of the sleeve when placed onto a mandrel allowed the team to make some decisions about next steps. Initially, a tendency for resin material adhesion to the tool threatened to disrupt flow coverage. However, by moving the sleeve side to side, the team decoupled the material, revealing the true champions: sleeves of medium thickness without a 20-degree exit. These sleeves allowed for seamless sleeve installation onto a mandrel within a one-minute timeframe, while simultaneously minimizing backflow to a drop. Based on these findings, the team determined that subsequent iterations should incorporate an extended length, ensuring complete mandrel coverage from the handle’s distal end to the bending point. This modification aims to optimize performance and address the observed sleeve installation time and flow coverage challenges.
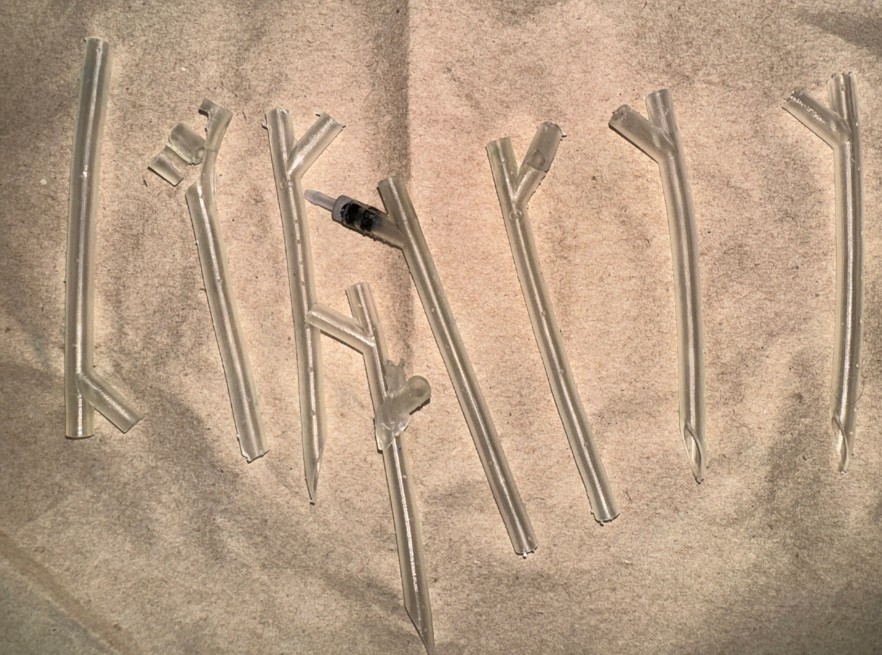