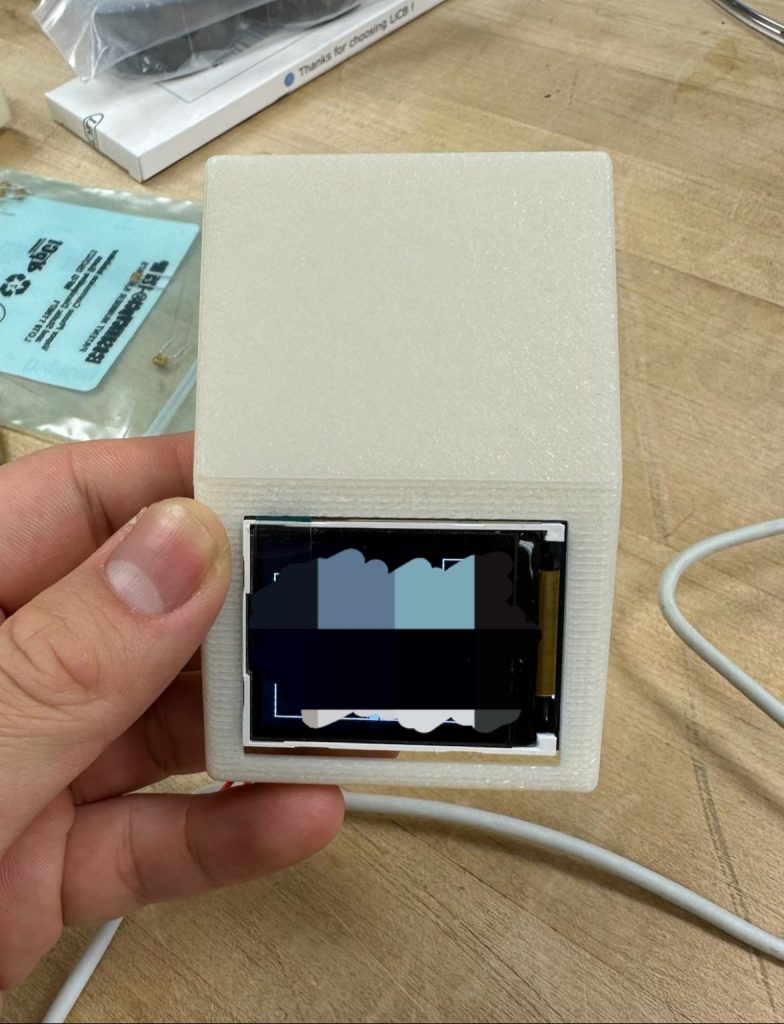
Over the past week, the team has made great strides towards a fully integrated prototype as the mechanical and electrical subteams increased collaborative efforts. For instance, a 3-D print of the housing from last week helped us generate a better idea of how electronics should be arranged to best fit (see the left example!). We are already working on the next housing iteration as remaining electrical designs and material selections are finalized.
The testing subteam has also taken valuable feedback from the QRB1 panel into consideration as the team continues to optimize our testing environment and procedure.
Finally, the team’s plans for the Final Design Review are slowly being developed as the team prepares to submit organized, high-quality final deliverables in April.